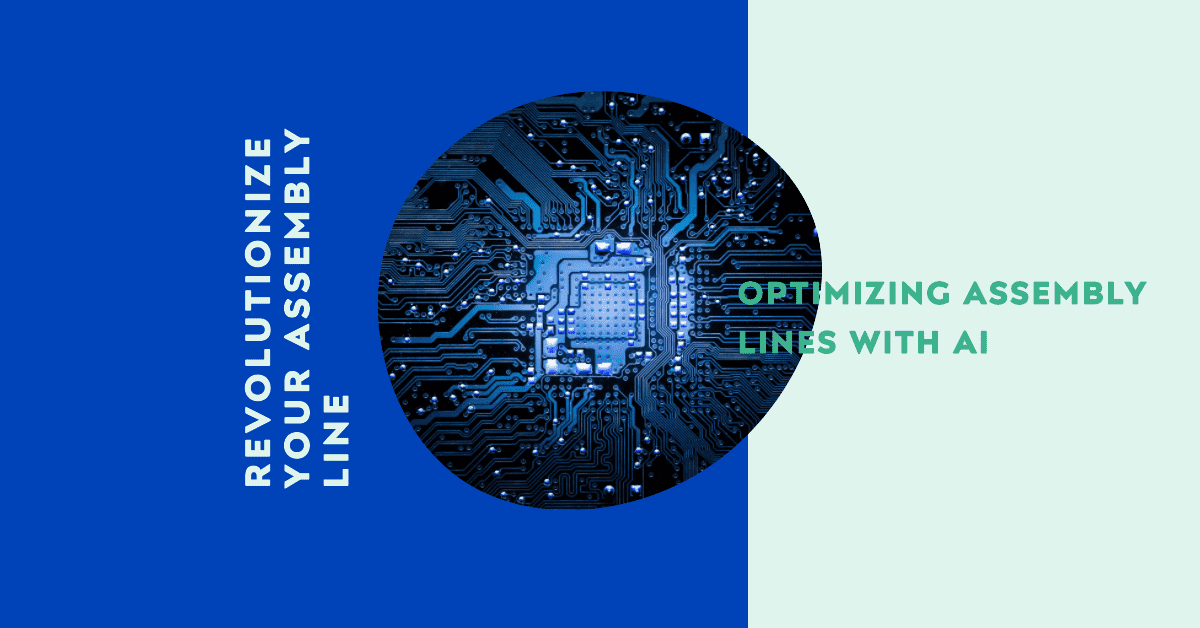
Part of the series: Applying AI in manufacturing
Manufacturing assembly lines are complex systems with many moving parts - both literally and figuratively. Effective assembly line optimization can lead to reduced costs, improved quality, and increased productivity. This is where AI comes in.
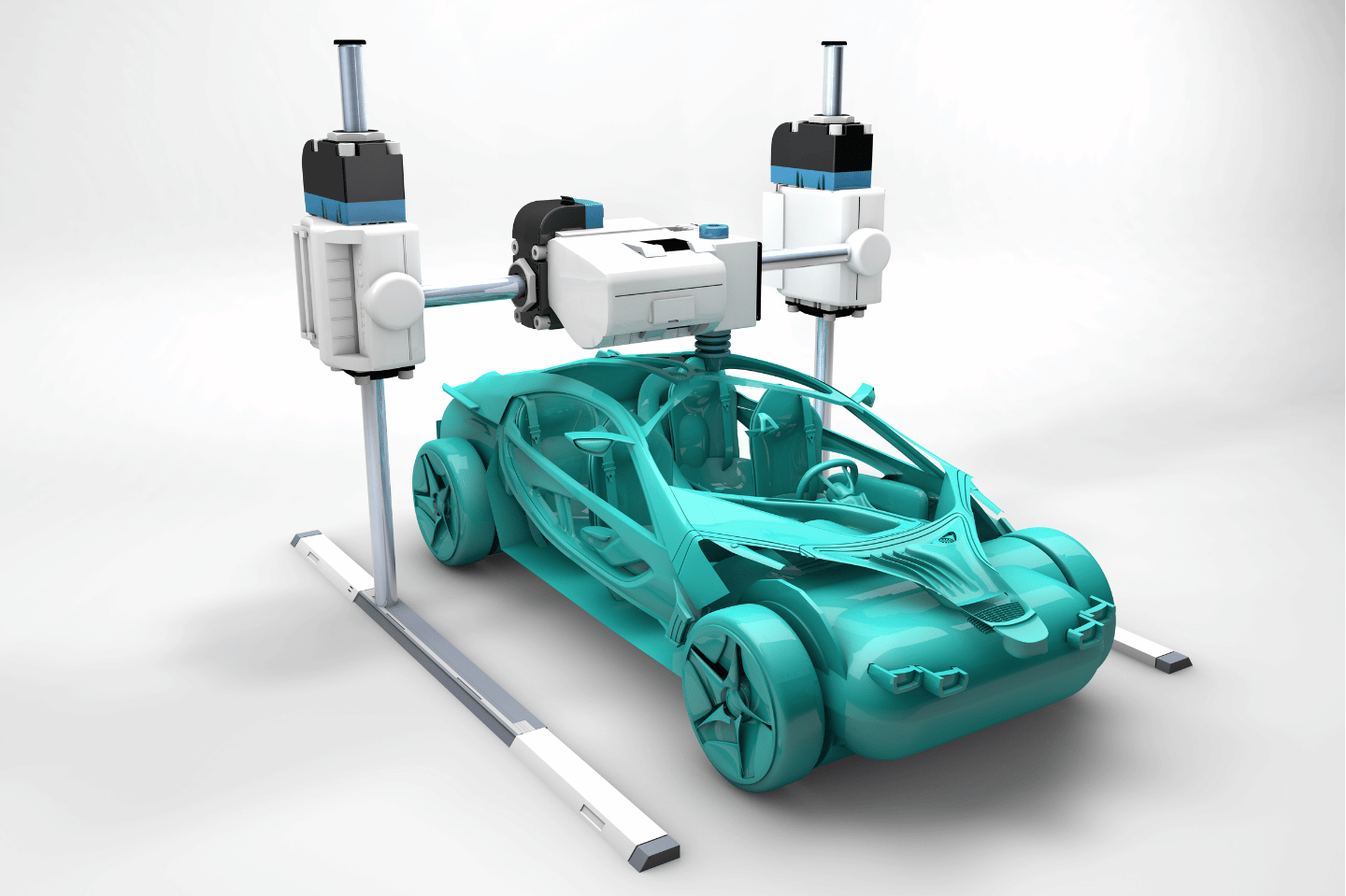
In this article, we'll explore how manufacturers can leverage AI and machine learning to optimize their assembly line operations. We'll look at use cases, benefits, challenges, and best practices. Let's get started!
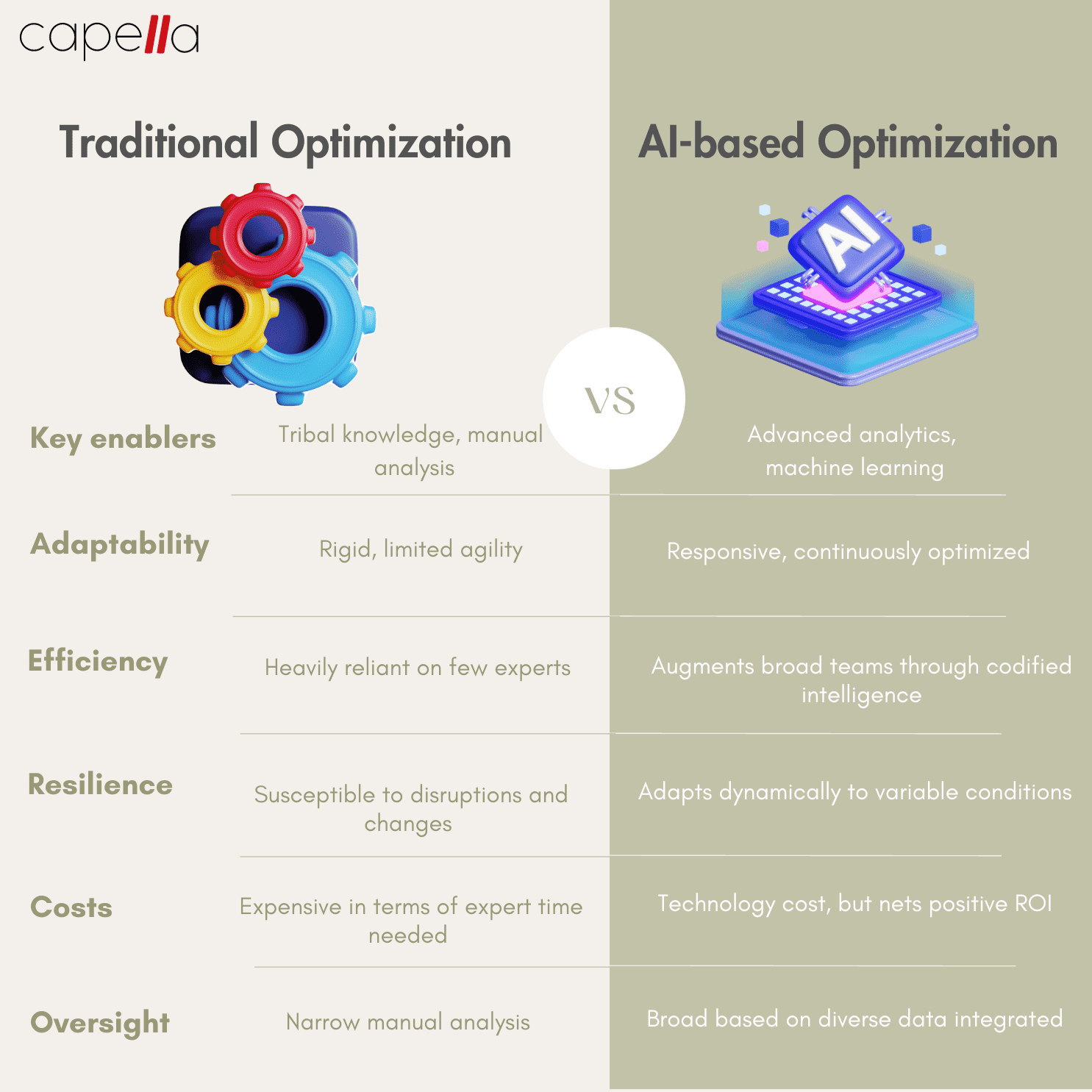
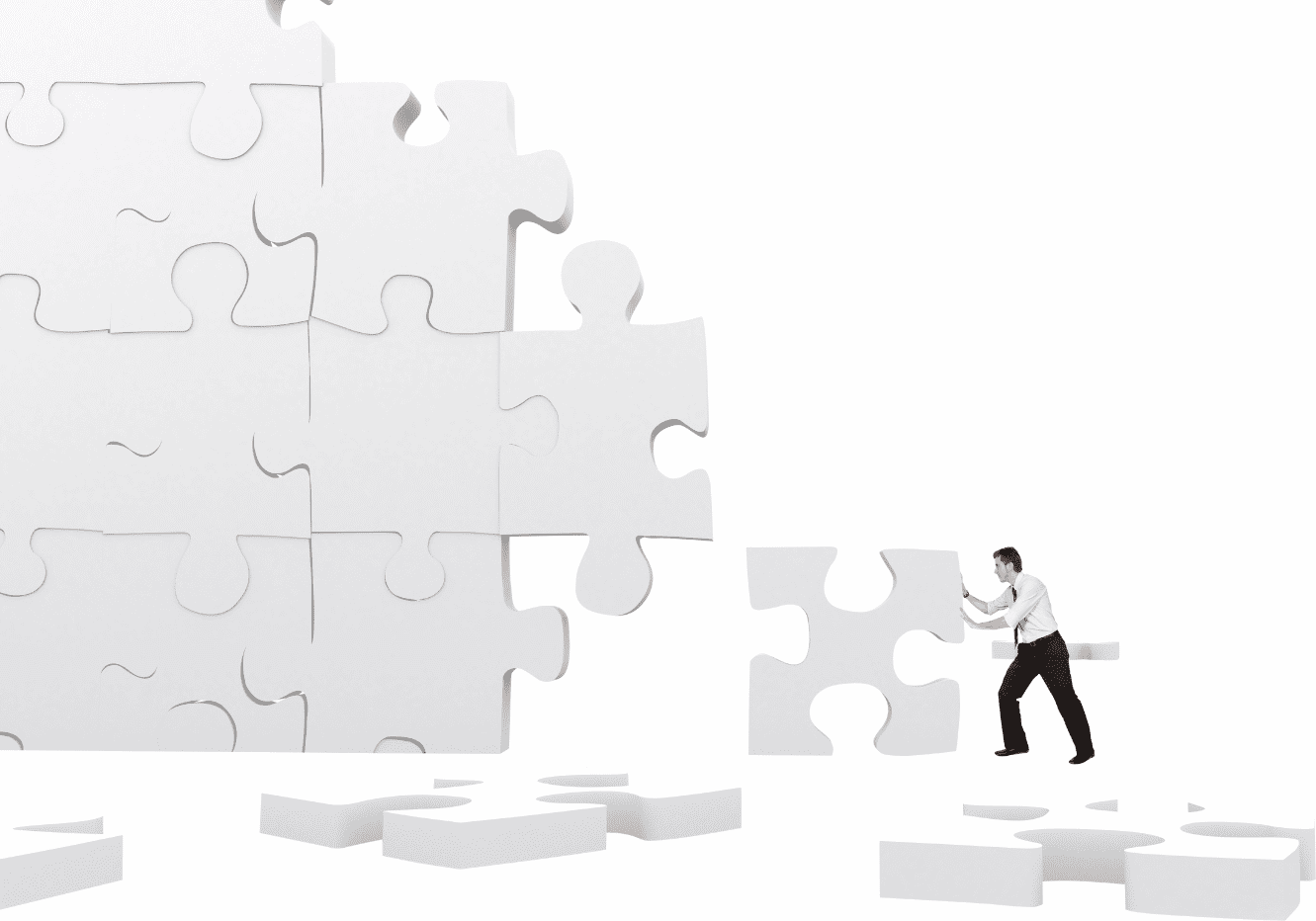
The challenges of traditional assembly line optimization
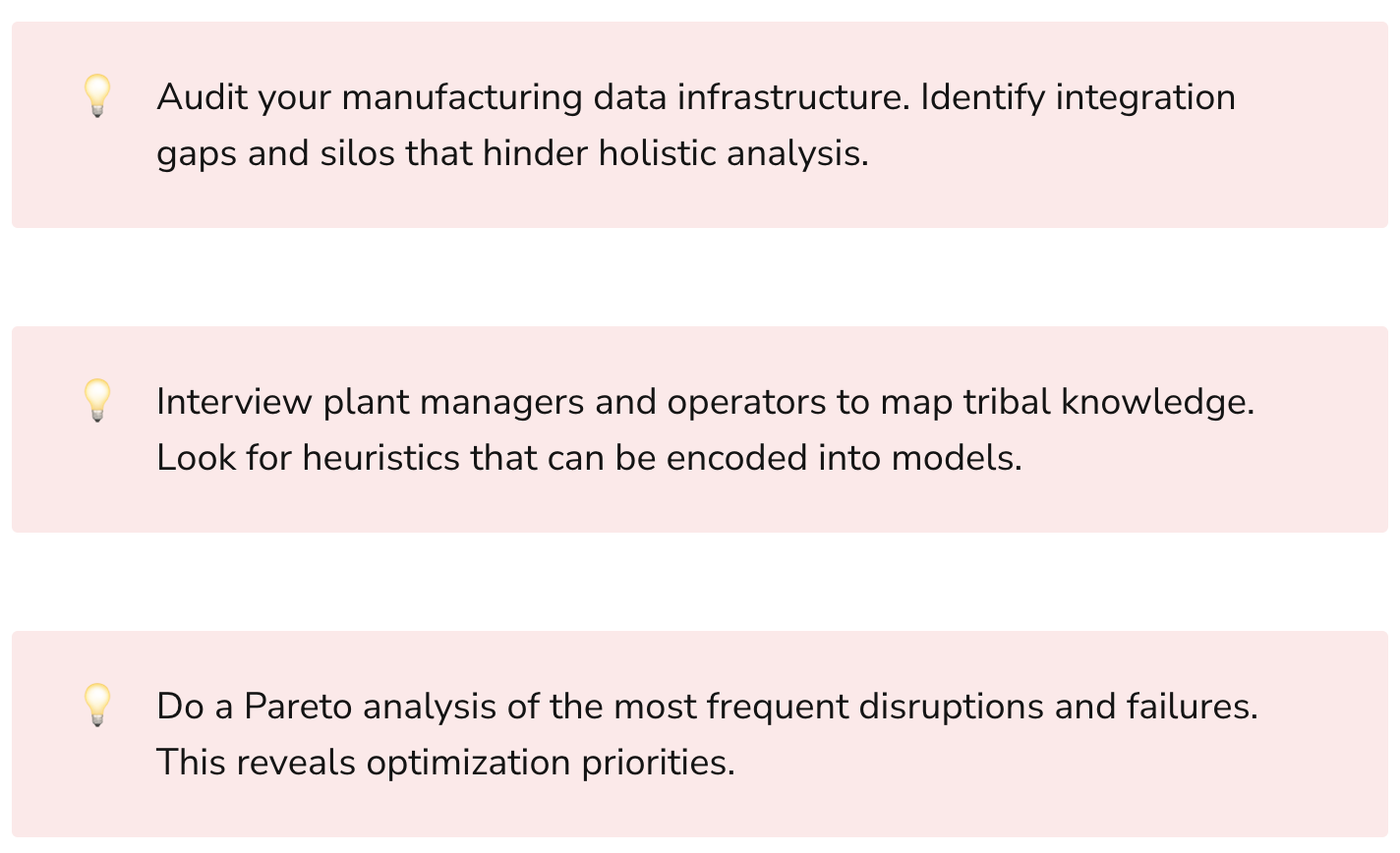
Assembly lines have been around for over a century, since the days of Henry Ford. The goals of assembly line optimization have remained largely the same - maximize throughput, minimize costs, reduce bottlenecks and waste.
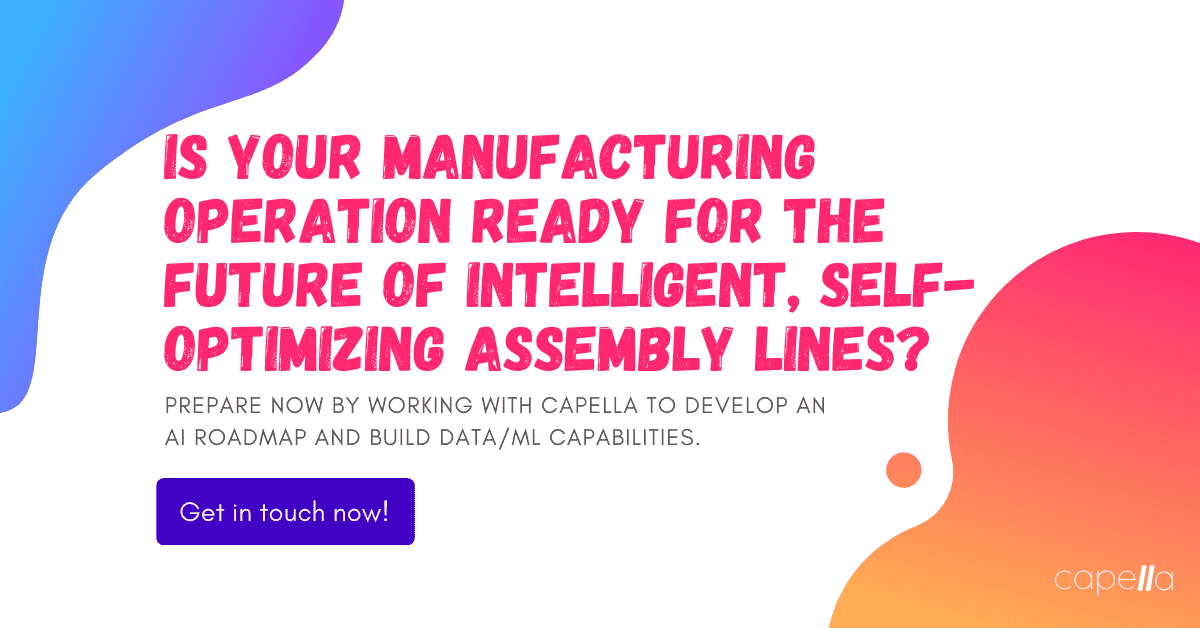
However, optimizing assembly lines is hard. Here are some of the challenges with traditional optimization approaches:
- Too many variables - Modern assembly lines have hundreds of configurable parameters - machine settings, environmental factors, product variants etc. Finding the optimal combination is incredibly complex.
- Dynamic conditions - Assembly lines operate in dynamic conditions. Small disruptions like machine failures, inventory delays or absenteeism can significantly impact productivity.
- Siloed data - Relevant data is spread across multiple siloed sources - sensor data, ERP systems, spreadsheets etc. Integrating these for holistic analysis is difficult.
- Manual approaches - Most optimization today relies on the tribal knowledge of experienced employees. But rules of thumb often fall short or fail to generalize.
- Black box systems - Many assembly line machines are closed systems with little visibility into their internal operations and instrumentation. Their performance is hard to model and improve.
Clearly, assembly lines exhibit the kind of complexity where AI can make an impact. Let's look at how.
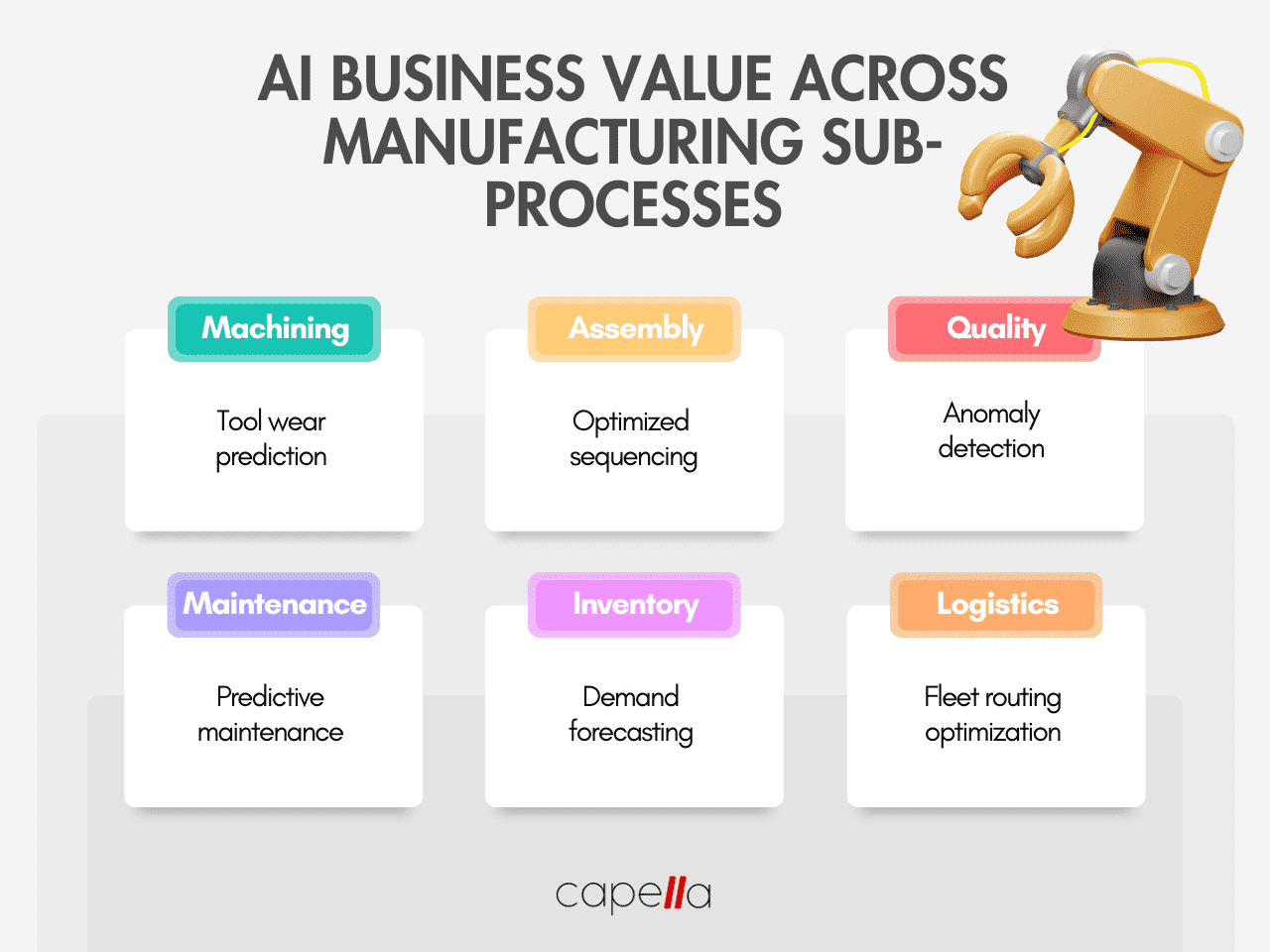
AI to the rescue
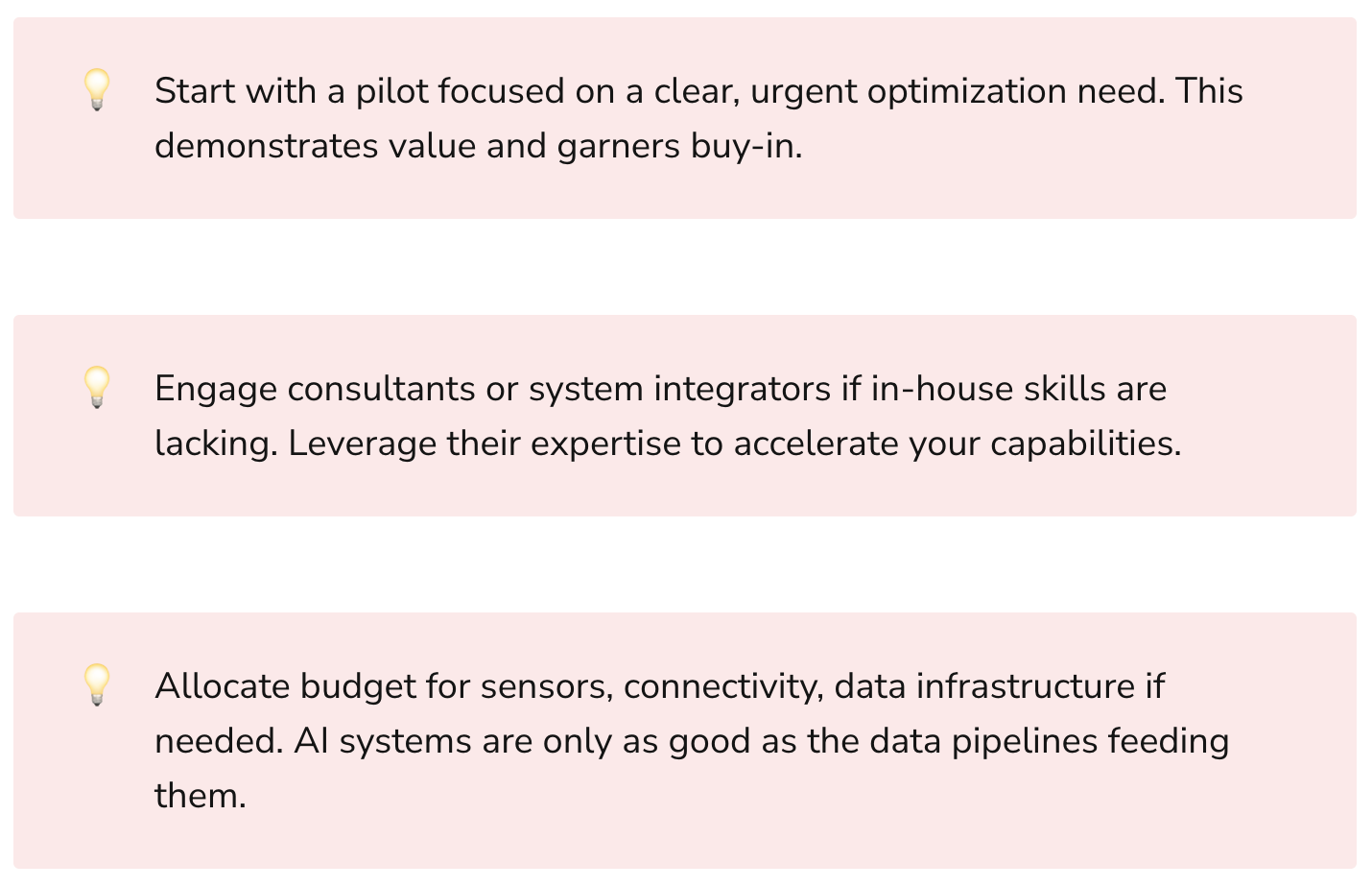
AI and machine learning techniques help address many of the challenges outlined above:
- Handle many variables - Algorithms like neural networks can model complex assemblies with hundreds of parameters and reveal optimal combinations.
- Adapting to dynamics - Online learning algorithms continuously train models on new data, allowing them to adapt to changing assembly line conditions.
- Integrate disparate data - MLaggregation and pipelines can combine and cleanse data from sensors, databases, spreadsheets and more into a unified representation.
- Democratize insights - Rather than rely just on expert intuition, data-driven models codify institutional knowledge and make it accessible to all.
- Open the black box - Behavioral modeling can infer the internal workings of equipment and systems in a data-driven manner.
Let's look at some real-world examples of AI-enabled assembly line optimization.
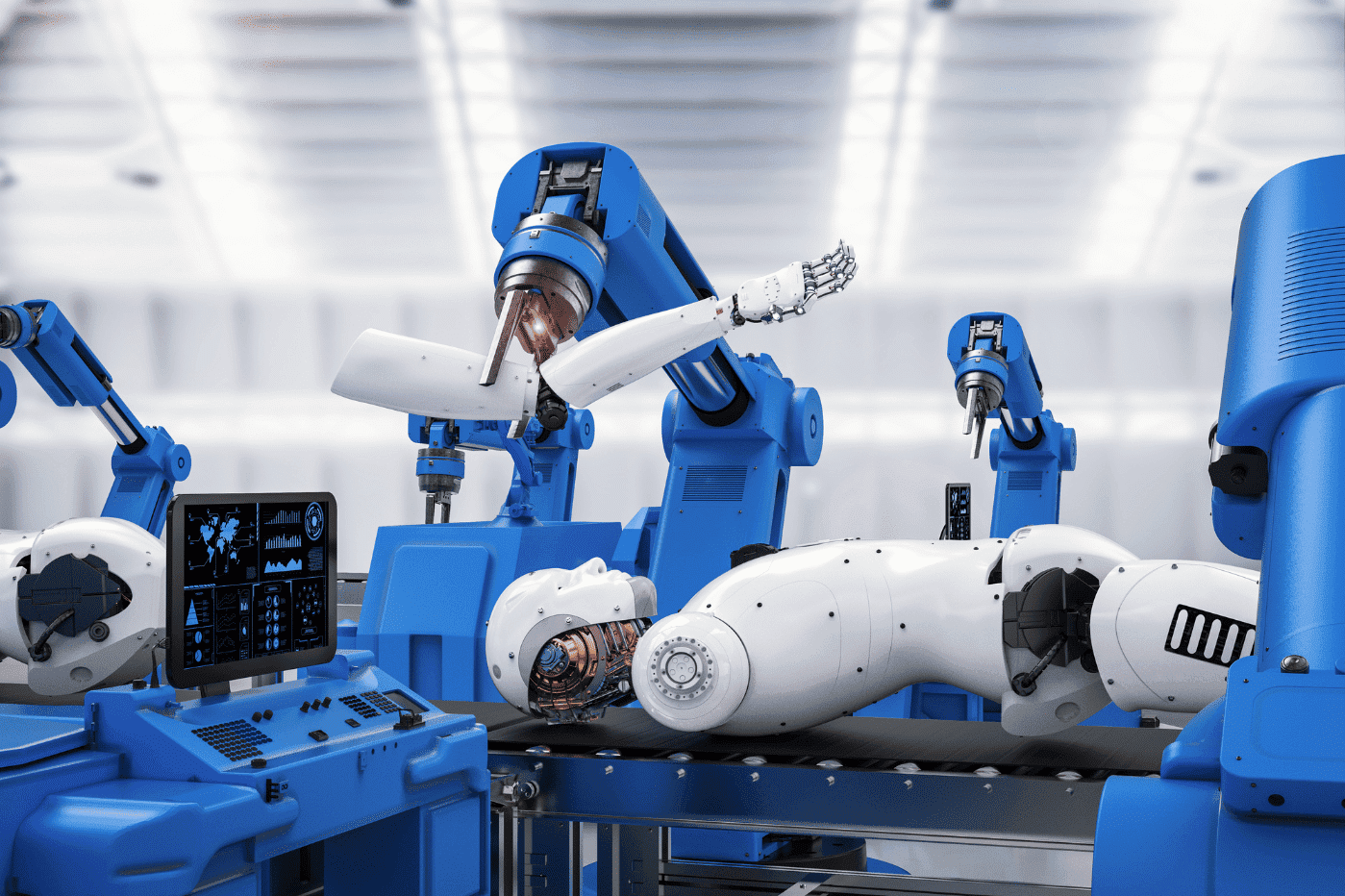
AI use case #1: Optimizing conveyor systems
Conveyor systems are the arteries of an assembly line, transporting parts between workstations and directly impacting overall throughput. However, manually optimizing conveyor velocity, segmentation (dividing the conveyor into zones), and gapping (spacing between parts) is a complex and time-consuming task.
AI-powered Optimization with Orchestrator AI:
Universal Robots partnered with Waypoint to utilize Waypoint's Machine Learning (ML)-based Orchestrator AI for conveyor system optimization. This innovative solution addresses the challenges of manual optimization through:
- Sensor Data Analysis: Orchestrator AI leverages data from various sensors on the conveyor system. This data might include belt speed, part location, and potential obstructions.
- Intelligent Modeling: The ML algorithms analyze the sensor data to create an intelligent model of individual conveyor segments.
- Parameter Tuning: Based on the model, Orchestrator AI automatically tunes conveyor parameters like velocity, segmentation, and gapping for optimal performance across the entire system.
Measurable Improvements:
Implementing Orchestrator AI has led to significant benefits for assembly lines:
- Increased Productivity: Production lines have seen productivity improvements ranging from 5% to 15%. This translates to a higher output with the same resources.
- Reduced Changeover Time: The time required to adjust the conveyor system for different production runs has been reduced by an impressive 90%. This allows for faster product transitions and greater production flexibility.
- Faster Time-to-Value: The solution offers a quick return on investment (ROI) due to its ease of integration with existing infrastructure. Existing conveyor systems can be readily optimized without major modifications.
AI use case #2: Dynamic line balancing
Achieving optimal production on an assembly line requires carefully distributing tasks across workstations. This, known as the assembly line balancing problem, is a continuous challenge for manufacturers. Here's why:
- Uneven Task Times: Assembly tasks can have varying durations depending on complexity or worker skill. Perfectly balancing lines with these variations is difficult.
- Station Downtime: Equipment breakdowns, worker breaks, and material shortages can create downtime at individual stations, disrupting the overall flow.
- Product Mix Changes: Manufacturing environments often produce a variety of products with different assembly requirements. This necessitates frequent line adjustments.
These factors lead to imbalances, where some stations have workers waiting for parts while others struggle to keep up. This reduces overall output and efficiency.
Capella's Adaptive Solution:
Capella offers an innovative approach called Adaptive Assembly Line Balancing. This leverages computer vision and machine learning (ML) to address the challenges mentioned above. Here's how it works:
- Real-time Monitoring: The system uses computer vision to track the Work-in-Process (WIP) inventory and throughput at each workstation in real-time.
- Dynamic Rebalancing: Based on the collected data, the ML algorithms can dynamically adjust task assignments across the line. This ensures stations are neither overloaded nor underutilized, optimizing overall performance.
The Benefits:
Capella's Adaptive Assembly Line Balancing solution has demonstrated significant benefits for manufacturers. Here's a specific example:
- Increased Output: A truck chassis assembly line saw a 20% increase in production output within just two weeks of implementing the system.
- Reduced Downtime: The time and resources spent on manual line rebalancing were reduced by 80%, leading to less disruption and improved efficiency.
- Cost Savings: The combined effects of increased output and reduced downtime contribute to significant cost savings through lower labor costs and improved resource utilization.
AI use case #3: Predictive maintenance
Unplanned machine failures are a major disruption to assembly line productivity. Traditional methods like Mean Time Between Failures (MTBF) offer a limited view of equipment health. They can't predict when a failure might occur, making it difficult to plan maintenance effectively.
Proactive Maintenance with Edge and Cloud Analytics:
Siemens SIMATIC offers a solution that leverages edge computing and cloud-based analytics for predictive maintenance. Here's how it works:
- Real-time Machine Monitoring: SIMATIC utilizes a network of sensors installed directly on machines (edge devices) to collect real-time data on various operating parameters like vibration, temperature, and energy consumption.
- Cloud-based Predictive Analytics: The sensor data is then transferred to a cloud-based analytics platform. This platform uses advanced algorithms to analyze the data and historical trends.
- Predictive Failure Models: Based on the analysis, SIMATIC builds predictive models that estimate the probability of failure for each machine component.
Benefits of Predictive Maintenance:
Implementing Siemens SIMATIC for predictive maintenance can yield significant benefits for assembly lines:
- Reduced Downtime: By identifying potential failures in advance, maintenance can be scheduled proactively, leading to a reduction in unplanned downtime by up to 15%, as demonstrated by an automotive OEM using the system.
- Optimized Maintenance Costs: Predictive maintenance allows for targeted maintenance actions, reducing unnecessary repairs and inspections. This can lead to cost savings of up to 8% on maintenance activities.
- Improved Overall Throughput: Reduced downtime and optimized maintenance schedules contribute to a smoother production flow, ultimately increasing overall throughput.
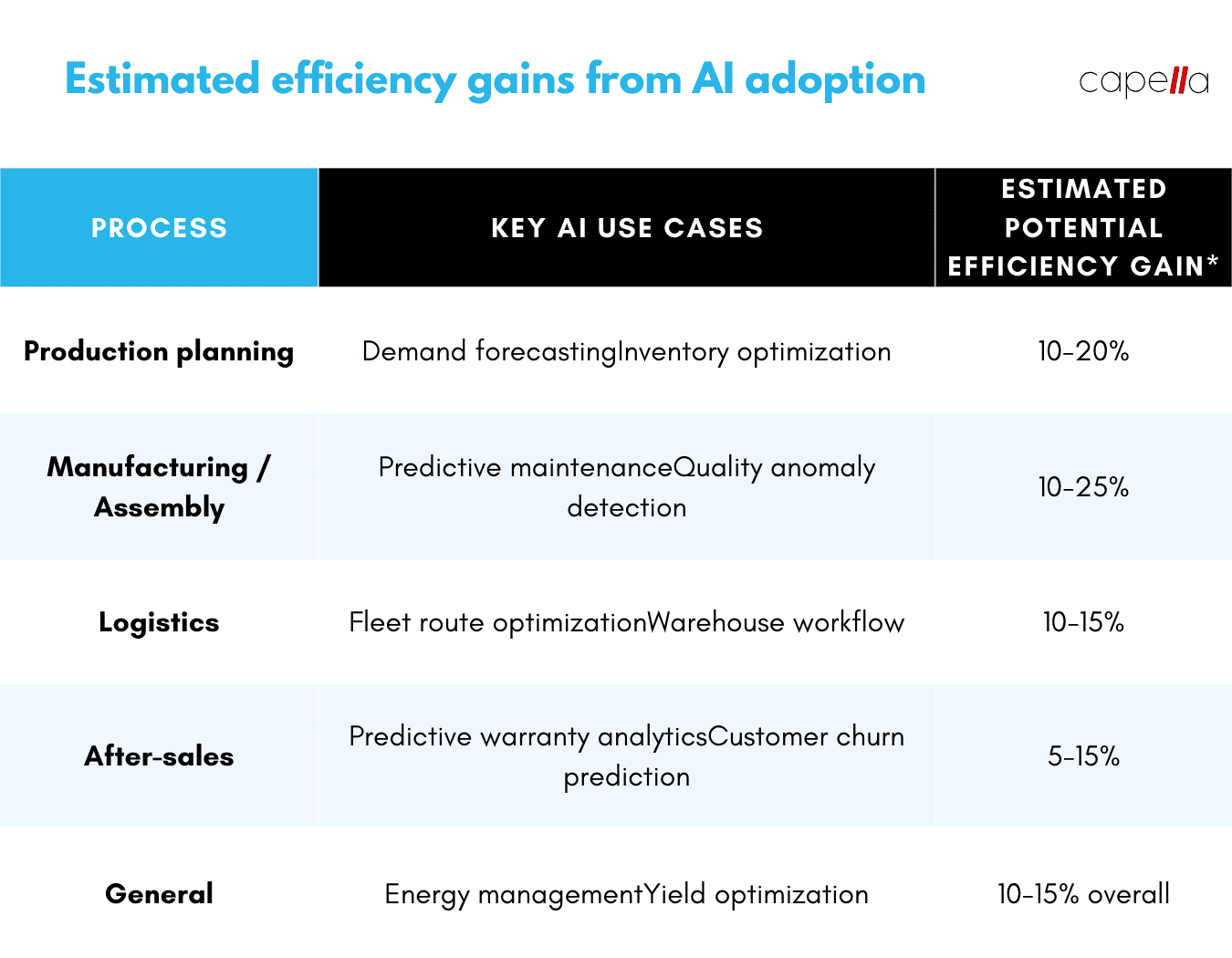
Realizing the benefits
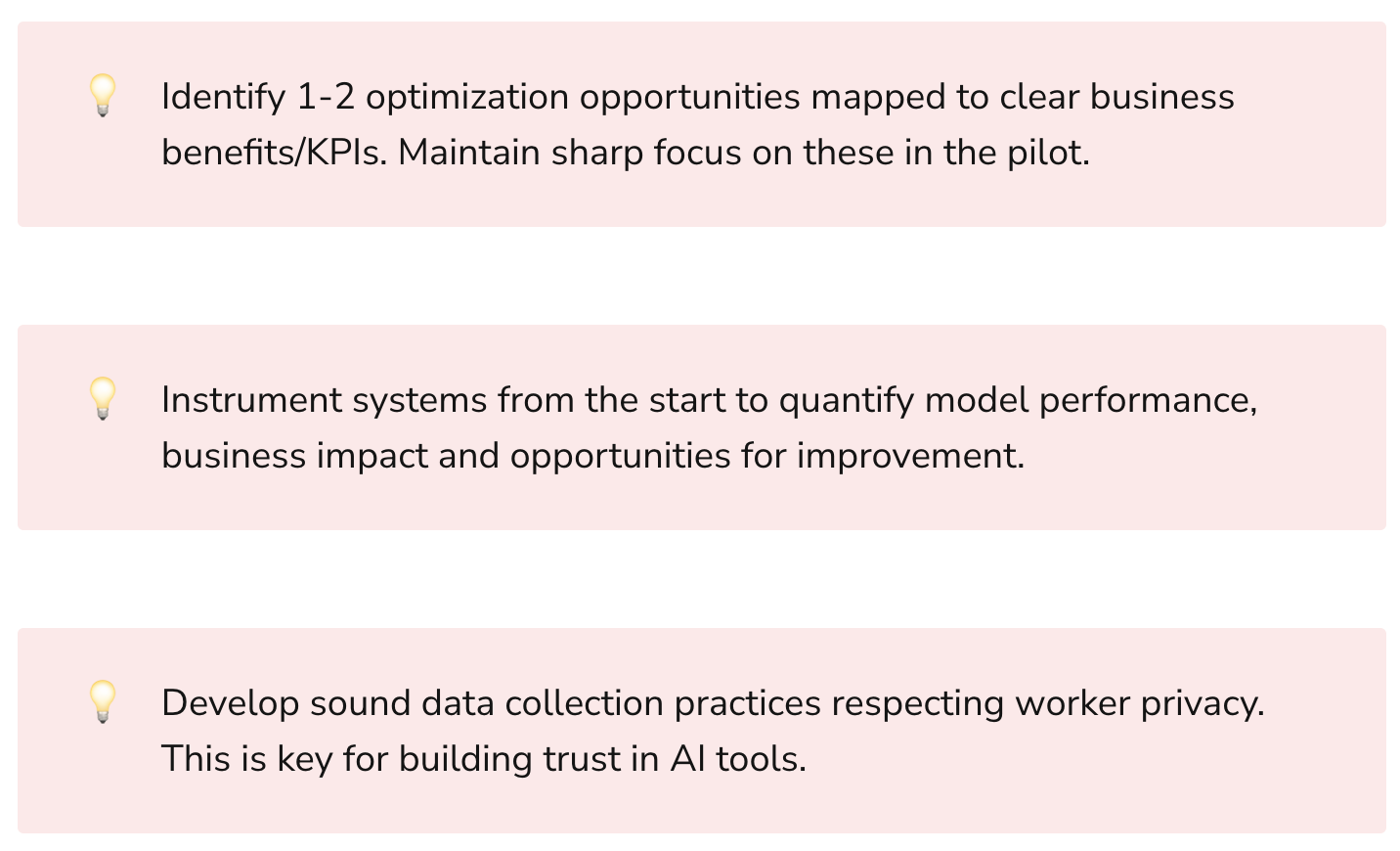
Here are some of the key benefits manufacturers can realize from AI-enabled assembly line optimization:
Higher throughput - AI helps maximize assembly line output through techniques like conveyor optimization, bottleneck reduction, dynamic balancing etc. Increased throughput directly translates to added revenues.
Lower costs - Reduced wastage, optimized resource use, energy savings and lower downtimes achieved via AI lead to significantly lower production costs.
Improved quality - AI models that predict failures, detect defects and recommend remedial actions help boost assembly quality and reduce rejects.
Faster changeovers - Machine learning aids rapid reconfiguration and balancing of lines to adapt to new product variants. This reduces changeover times.
Reduced downtime - Predictive maintenance powered by AI slashes unplanned downtime and associated losses by alerting in advance of equipment failures.
Enhanced flexibility - Data-driven models make assembly lines far more flexible and adaptive to disruptions compared to rigid manual solutions.
Consistent optimization - Unlike humans, AI systems don't get tired or bored! They consistently optimize operations 24x7.
The common thread across these benefits is driving efficiencies across assembly line operations via applied intelligence. But as with any technology, there are some limitations to consider.
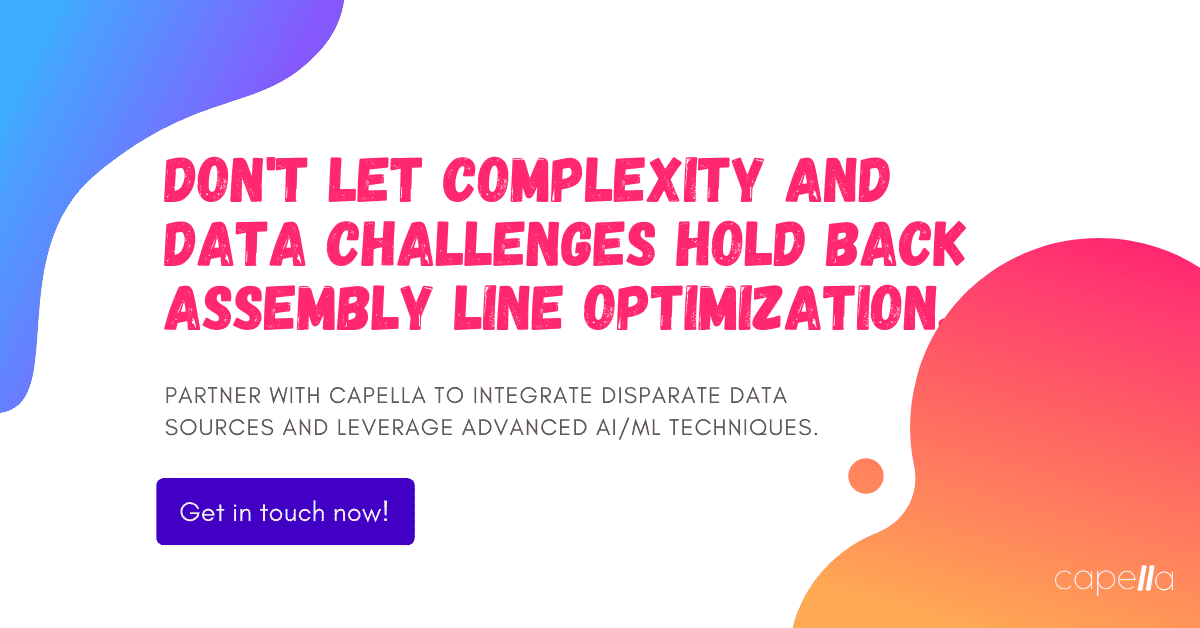
Challenges in implementing AI
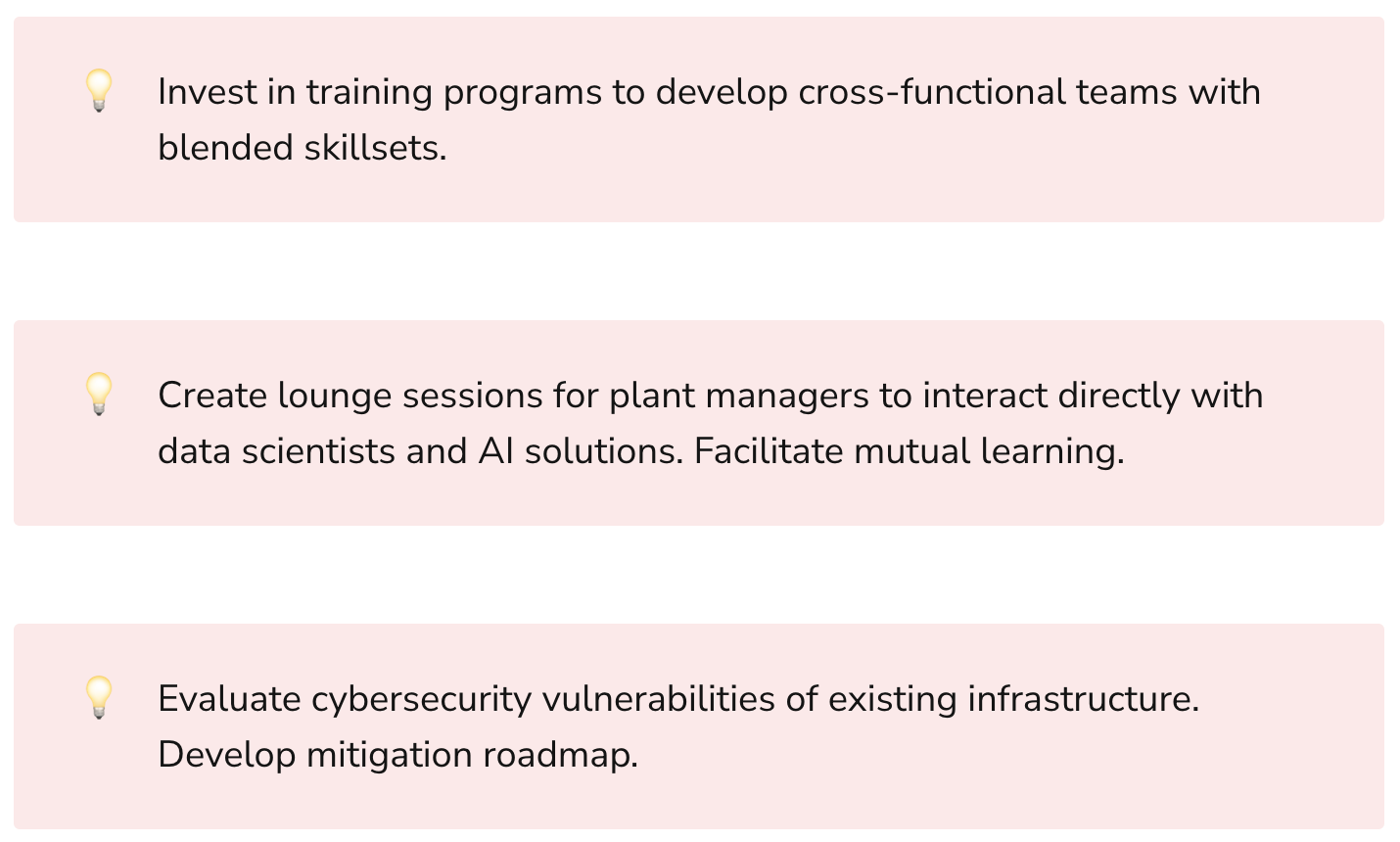
While promising, AI-driven assembly line optimization also comes with a unique set of challenges:
- Requires large volumes of quality data for model training and validation. Lack of data can hamper adoption.
- Assembling the multi-disciplinary skills needed - data engineering, OT/IT integration, data science, UI design etc.
- Cultural inertia against deploying black box systems for optimization, especially in regulated industries. Need to enable trust and transparency.
- Potential cybersecurity vulnerabilities by expanding the attack surface. Securing connected machines and infrastructure is critical.
- Challenges in integration with diverse existing assets and infrastructure across factory sites.
- Business processes must evolve to leverage AI-driven optimization recommendations. Ignoring model outputs negates ROI.
However, these challenges are not insurmountable. A systemic approach can help tackle them. Here are some best practices manufacturers should follow:
Best practices for implementation
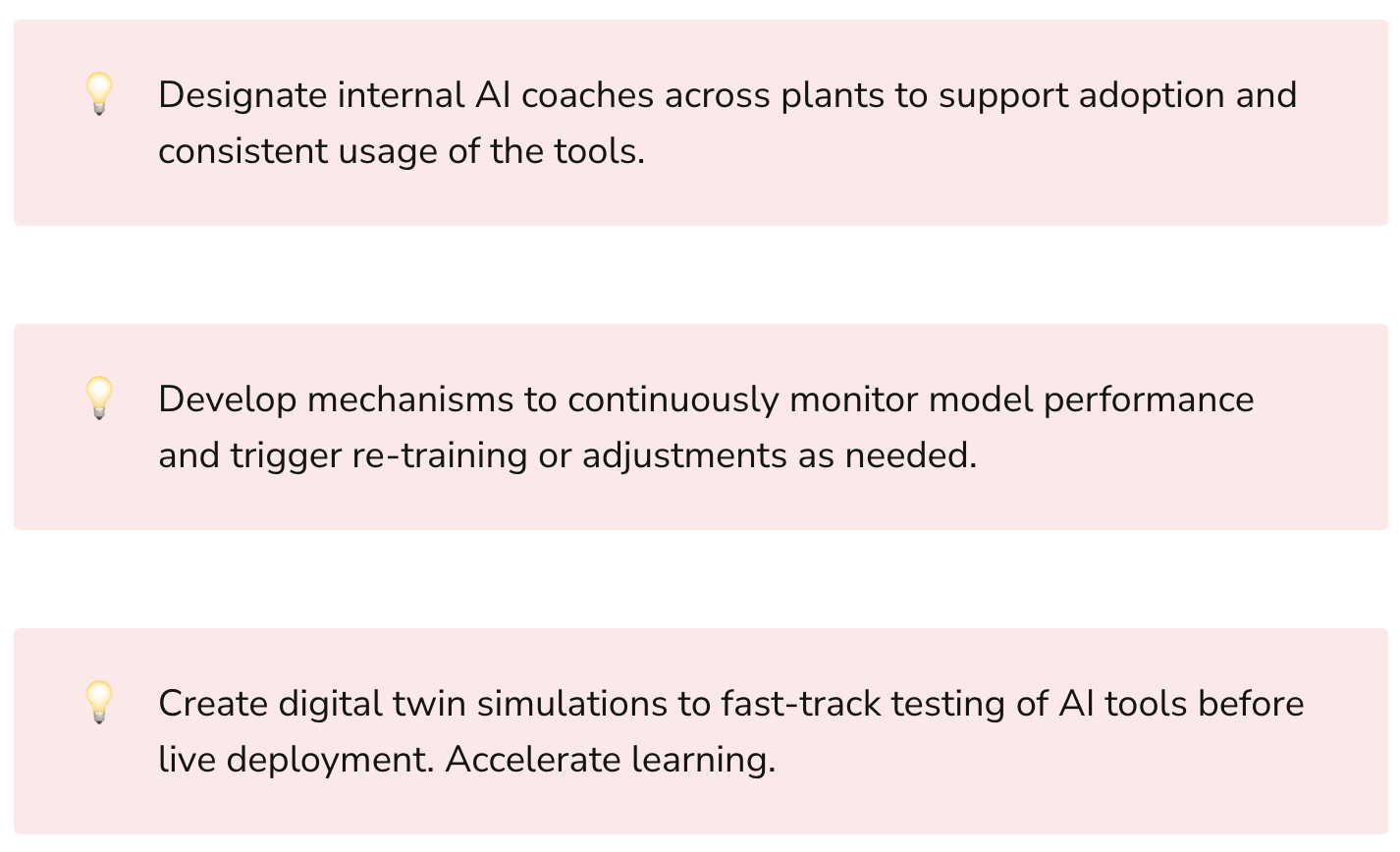
- Start small, but think big - Run pilot projects with limited scope that demonstrate quick wins. But have a long term roadmap to expand and integrate.
- Focus on data pipelines - Strong data infrastructure and pipelines are crucial to fuel AI systems. Allocate sufficient resources here.
- Train hybrid teams - Develop talent bench with cross-functional skillsets spanning OT, IT, data engineering, data science and more.
- Co-create solutions - Collaboratively develop solutions with a diverse project team including corporate IT, OT engineers, domain experts, data scientists etc.
- Educate stakeholders - Help stakeholders like plant managers understand what AI is (and isn't) via education and clear communication.
- Enable transparency - Provide domain experts visibility into model features and training data to build trust.
- Plan for edge deployment - Design solutions for edge deployment where possible to minimize latency, cyber risks and cost.
- Iteratively refine - Models and systems need constant measurement, monitoring and improvement. Build institutional mechanisms to enable this.
The road ahead
Intelligent, self-optimizing assembly lines powered by AI represent the future of manufacturing. This technology is no longer in the realm of science fiction. From predictive maintenance to conveyor optimization, leading manufacturers are already realizing hard benefits.
But there is significant headroom for broader adoption across factory floors. As platforms mature, skills develop and best practices proliferate, AI-enabled optimization will progress from isolated use cases to standardized solutions. And assembly lines worldwide will unleash data-driven intelligence to maximize productivity and quality.
The technology is already here. The opportunity is now. The road ahead is one of tremendous potential to realize the promise of AI in manufacturing. Let's keep learning, collaborating and innovating to travel down this road - together!
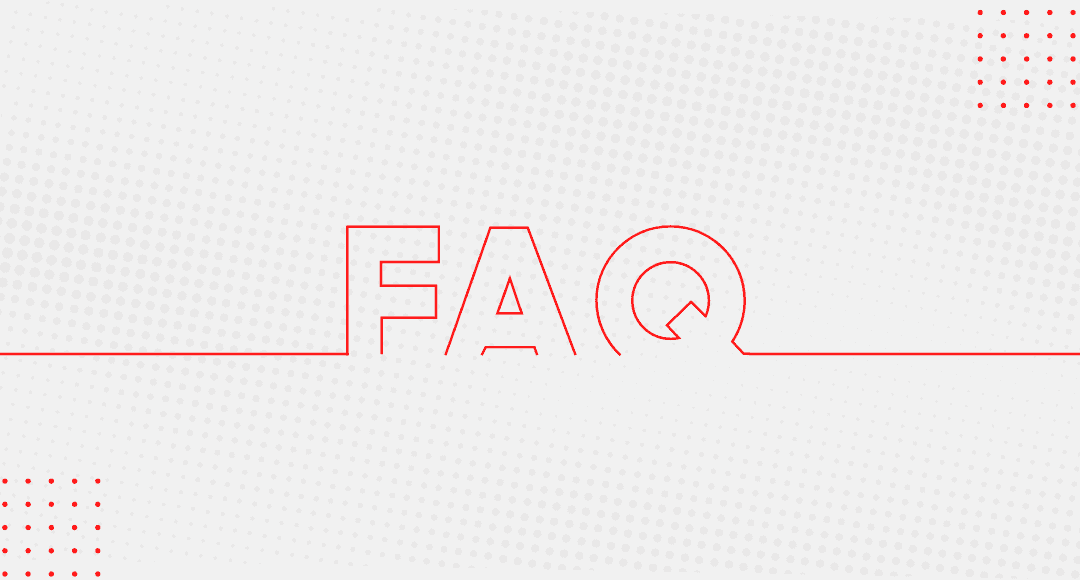
1. How can AI optimize our assembly line if every line is unique?
While each assembly line is unique, they share common characteristics like workflows, bottlenecks, changeovers etc. where AI can drive major impact. With good data infrastructure, AI models can be trained to adapt to specific line configurations. The key is starting with a pilot focused on a clear optimization goal before scaling.
2. What kind of data do we need to implement AI on the assembly line?
You will need diverse datasets - sensor data from equipment, process logs, records of downtime, output quality, inventory flows and more. Much of this likely already exists in siloed systems. The key is integrating it all into consistent, timestamped datasets for AI model training and inference. Strong data pipelines are critical.
3. Our assembly line uses a lot of proprietary and legacy machines. Will AI work with them?
Yes, AI can deliver value even with legacy and closed machines by using external sensors and behavioral modeling. For example, power consumption patterns can indicate upcoming failures without needing access to internal systems. But having API access and instrumentation helps AI deliver higher impact.
4. How long does it take to see results from AI deployment?
The first priority is building robust data infrastructure and pipelines to feed the AI systems. This can take weeks or months depending on starting maturity. Once this foundation is set, pilots focused on urgent optimization needs can show dramatic improvements within weeks or months. Scaling the solutions across lines and processes takes longer based on priorities.
5. What are the biggest challenges in implementing AI for assembly lines?
Top challenges include data integration across diverse sources, lack of internal skills, cultural inertia against deploying black box systems, cybersecurity risks of connected infrastructure, integration with legacy systems, and business process alignment to leverage AI outputs. Manufacturers must tackle these systematically.
6. Who needs to be involved in an AI optimization project?
Success requires a cross-functional team spanning corporate IT, plant engineers, maintenance technicians, OT specialists, data engineers, data scientists, line managers, operators and more. Avoid the mistake of having IT or data scientists work in isolation.
7. How can we ensure AI models keep improving over time?
The key is implementing strong closed loop processes for constant measurement, monitoring and improvement. Models must be retrained periodically on new data. Their performance relative to KPIs must be tracked. Feedback loops to enhance training data quality and model logic are vital.
8. What cybersecurity aspects are critical for AI on the assembly line?
With added connectivity of operational infrastructure, cyber risks increase. Securing connected machines, encrypting data transfers, controlling access, and monitoring for anomalies are crucial. Cybersecurity must be baked into solutions from the start, not bolted on later.
9. How can manufacturers develop the skills needed to maximize value from AI?
Training programs focused on digital and data skills are vital to build internal capabilities. But also leverage external partners strategically for specialized skills like data engineering, data science and OT/IT integration. Take a hybrid approach balancing internal learning and external partnerships.
10. What are the biggest lessons from early AI optimization implementations?
Key lessons include starting small but scaling fast when pilots show value, having sharp focus on urgent optimization needs with clear ROI, cobbling together multi-disciplinary skill sets, engaging domain experts throughout, investing heavily in data infrastructure, and measuring/monetizing business impacts for continued buy-in.
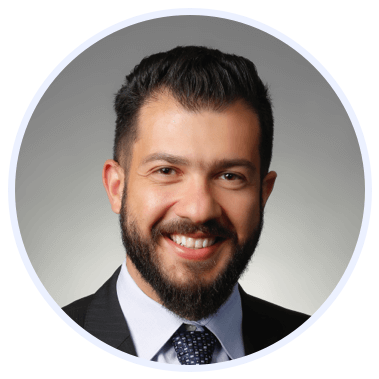
Rasheed Rabata
Is a solution and ROI-driven CTO, consultant, and system integrator with experience in deploying data integrations, Data Hubs, Master Data Management, Data Quality, and Data Warehousing solutions. He has a passion for solving complex data problems. His career experience showcases his drive to deliver software and timely solutions for business needs.