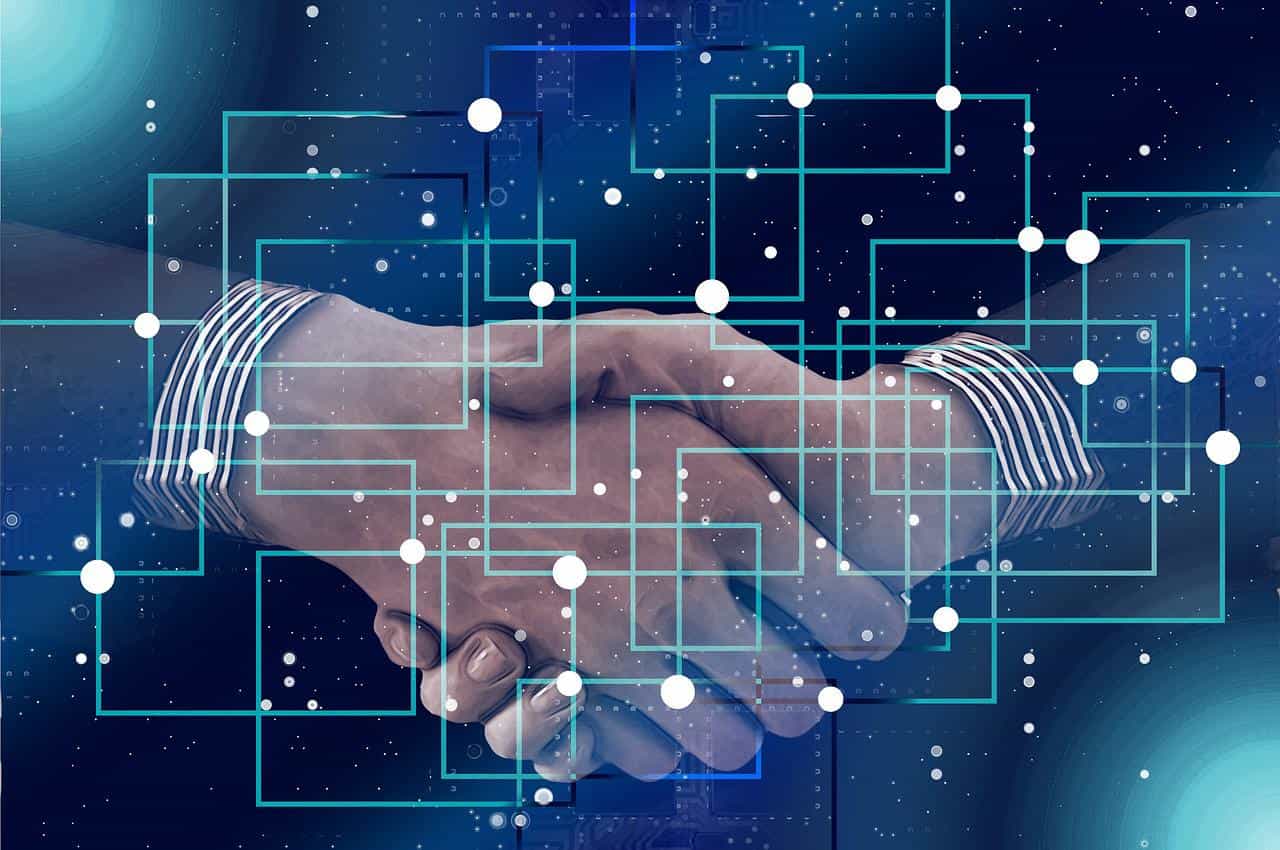
Manufacturing companies are constantly challenged by the need to keep up with customer demands, improve efficiency, and reduce costs. Data, when accurate, has proven its worth for the executive team in driving processes to be more efficient and providing guidance for improven. However, more often than not, efforts at using data fail when data quality standard doesnt meet expectation, eroding trust and undoing progress quickly.
You can build the best visualizations in the world, but if you don’t trust the underlying data, you won’t be able to trust the results of your efforts or make sense of it. High-quality data is the essential ingredient for high-quality analytics and driving decisions or automation based on it. This is where data management can help manufacturers meet these challenges by improving their ability to access key data that can be trusted and drive business processes based on it.
One common data management practice, is having a master data hub (MDM). An MDM is critical for manufacturing because it helps ensure that your organization has a consistent and up-to-date understanding of the main entities: customers, vendors products and processes that drive their business from different departments in one place.
MDM is more than just a data governance initiative. When you're dealing with millions (or even billions) of pieces of information, you need to know that every bit is accounted for, categorized correctly, and ready to be used whenever you need it.
Without master data management, you could end up with:
- duplicate customers records in your database;
- incorrect information being used in reports;
- inaccurate sales reports;
- products missing from inventory;
- product packaging errors.
Master Data Management is a crucial part of any manufacturing company's ongoing success. Here are just a few reasons why:
An MDM system is at the center of manufacturing operations.
MDM is the glue that holds all other systems together, and it provides a single source of truth for your business.
- A centralized MDM system serves as the information hub for manufacturing, providing data about products and processes that drive improvements in machinery, automation, and scheduling.
- In an MDM system, you can create a baseline view of your entire operation by collecting data from multiple sources to produce comprehensive information about what's happening within each process, including supplier quality data; equipment performance statistics; production line efficiency metrics; labor hours per item produced (if applicable); etc.
Manufacturers have been used to silos for a long time.
If a business has lots of silos—loads of disconnected, isolated departments that don’t talk to each other—it will struggle to make efficient use of its data. This is especially true for manufacturers, who have been used to working in this way for so long that it’s second nature for them.
But it doesn’t have to be this way. With data integration and management tools like Master Data Management (MDM), companies can eliminate their silos and finally bring all their disparate parts together into one cohesive whole.
MDM technology works by identifying what data is shared between different departments or divisions within your business and unifying those pieces into a single source accessible across your entire organization through an intuitive interface that makes finding what you need easy no matter where it lives or how many times it has been rebranded over time (or both).
An MDM system creates a single source of truth.
MDM systems create a single source of truth. This means that all information related to the same product, customer, or supplier is stored in one place, with a unique identifier and at least one piece of metadata for each record. In other words, if you’re looking for a specific record in the database, you can find it easily because the MDM system has created an index out of all the relevant attributes from all related records.
With this kind of accuracy and efficiency built into their systems, manufacturers can use MDM software to drive business intelligence (BI), business continuity planning (BCP), and business process improvement (BPI). They can also use it as part of their efforts towards business transformation through better governance over processes involving time-sensitive data like that used by factories or construction sites.
Manufacturing has unique data needs, which aren’t met by point solutions.
Manufacturing companies of all sizes have unique data needs. Their transactional data, such as sales orders and bills of materials are dynamic, requiring frequent changes to ensure accuracy. And their more-static data, such as product and customer definitions are scattered across numerous systems often resulting in significant time lost to data reconciliation efforts.
Engineering and purchasing are silos of information, with data residing in a plethora of tools that can be accessed in only one way. That’s the problem. It’s the reason manufacturers often spend more time completing requests and manually keying data than they do looking at big data to identify trends, extract insights, and act on them.
Point solutions are well-suited for solving business problems with limited scale and scope. But as companies grow, these discrete systems become inflexible and can’t adapt to new requirements or deliver rich insights.
This is where MDM gives companies a central repository for handling all their master data. This is important because it saves companies money and their time in the long run — not to mention that it increases efficiency in the short term.
Master data management is an iterative process that can bring huge benefits to your business.
Master data management is an iterative process. It can bring huge benefits to your business, but it's not a one-time event.
For example, you might start by setting up a master data hub to centralize your organization's most important data sources, including customer information and supplier information. Then you could implement a governance framework that ensures all products have consistent descriptions across all systems in your enterprise.
After these first steps are completed, you may want to expand the scope of your MDM program by adding more detailed product specifications (for example, technical specifications for each of your products) and setup procedures for new employees on specific product lines or sectors within the company (such as sales). This will take some time and money—but if done properly from the beginning it will be worth it!
A master data management system can dramatically improve your manufacturing operations.
Master data management is a foundational element for manufacturing. It's a key component of the manufacturing supply chain, and it is a critical tool for manufacturers who want to use analytics to improve their operations. MDM is also an essential component of enterprise architecture because it allows manufacturers to align all their business processes, including those in the purchasing department, with their overarching objectives and goals.
For example, if you're trying to reduce your environmental footprint by reducing waste and energy consumption at your factory or distribution center but don't have centralized control over your data assets across departments or locations—or if you don't know what products are being produced where—you won't be able to measure progress toward achieving your sustainability goals or make any changes when necessary.
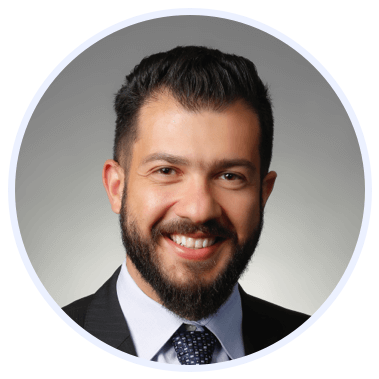
Rasheed Rabata
Is a solution and ROI-driven CTO, consultant, and system integrator with experience in deploying data integrations, Data Hubs, Master Data Management, Data Quality, and Data Warehousing solutions. He has a passion for solving complex data problems. His career experience showcases his drive to deliver software and timely solutions for business needs.