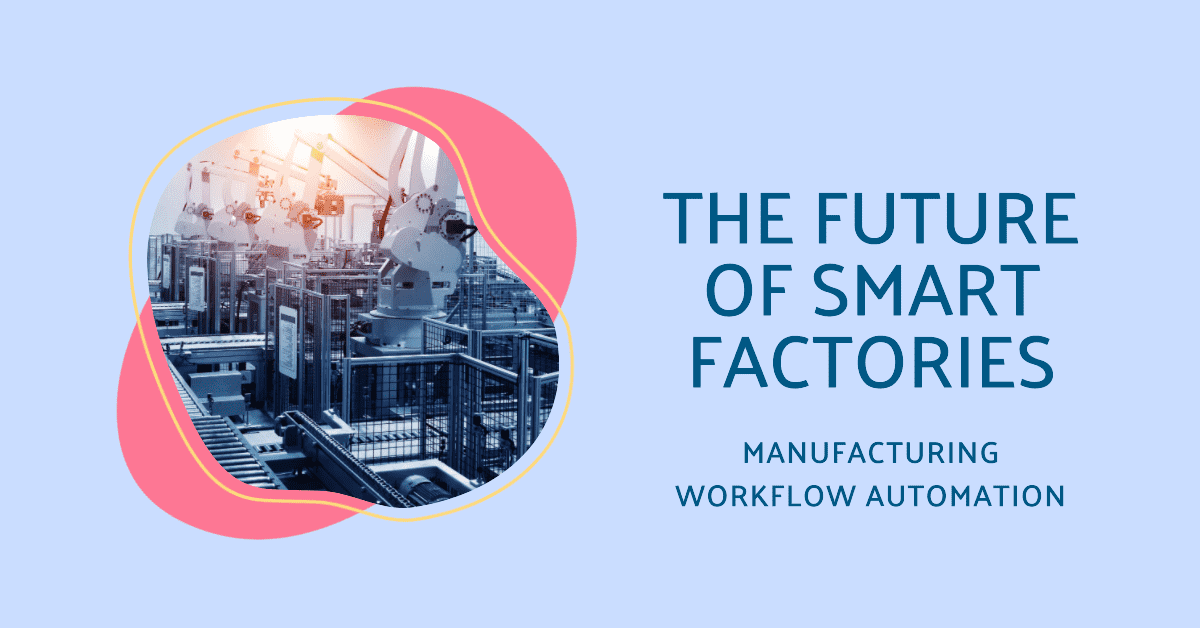
The manufacturing industry is undergoing a digital transformation. With advances in connectivity, sensors, artificial intelligence, and automation, manufacturers can collect and analyze data to optimize production in new ways. One key technology that is enabling this transformation is manufacturing workflow automation.
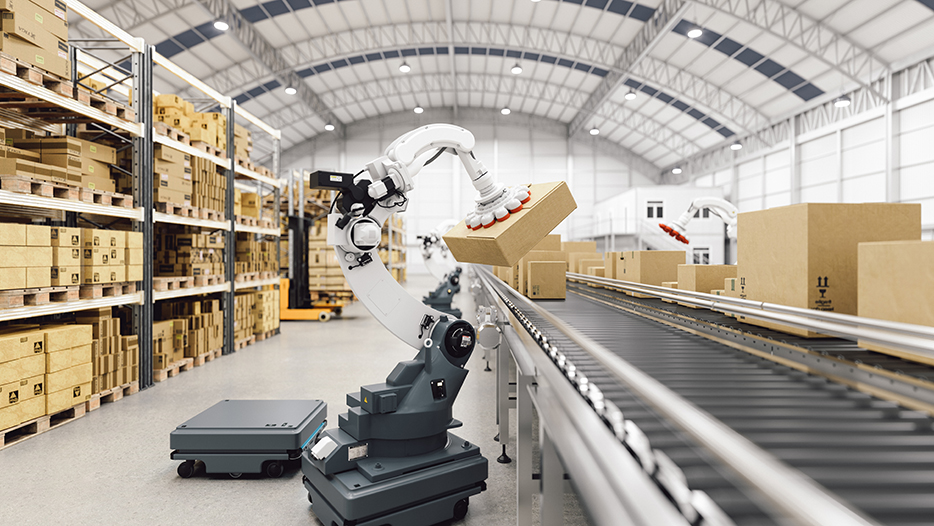
What is Manufacturing Workflow Automation?
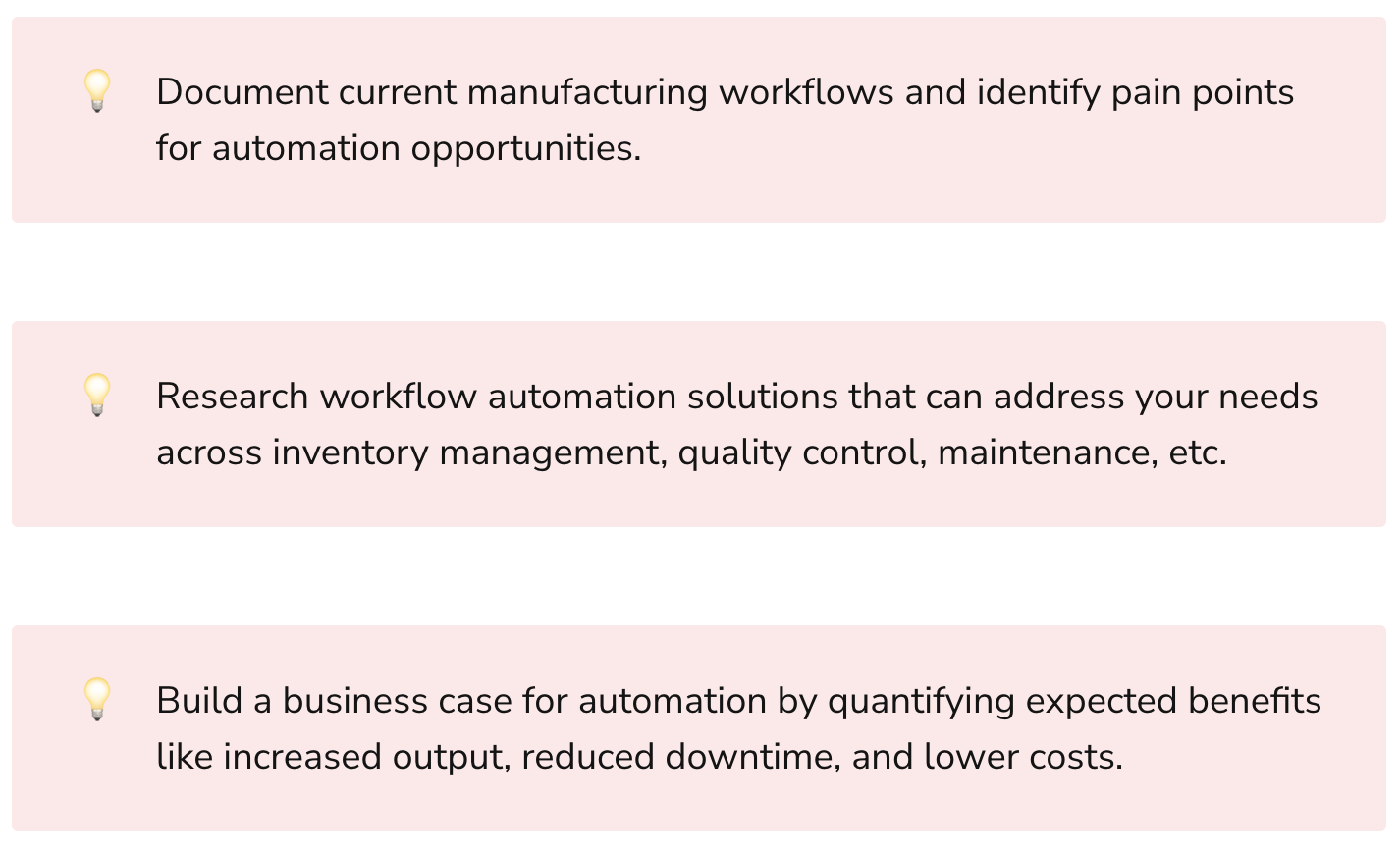
Manufacturing workflow automation refers to using software and automation tools to manage and optimize manufacturing processes and workflows. The goal is to improve efficiency, quality, and consistency while reducing errors and waste.
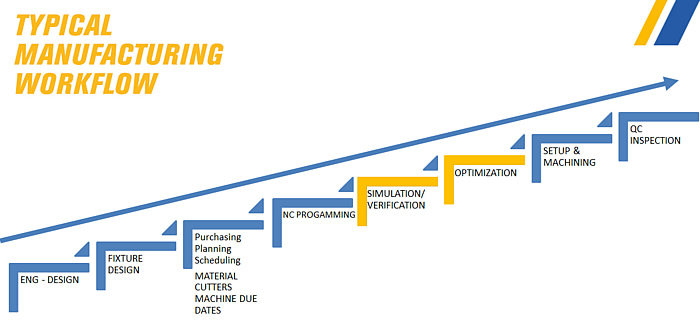
Some common examples of manufacturing workflow automation include:
- Automated production scheduling and sequencing
- Inventory management and stock replenishment
- Quality control and defect reduction
- Predictive maintenance and asset management
- Supply chain and logistics optimization
- Production monitoring and analytics
- Workflow standardization and process mining
These applications rely on technologies like sensors, robotics, machine vision, AI, and advanced analytics. When integrated together into an automated system, they can optimize the flow of materials and information throughout a factory.
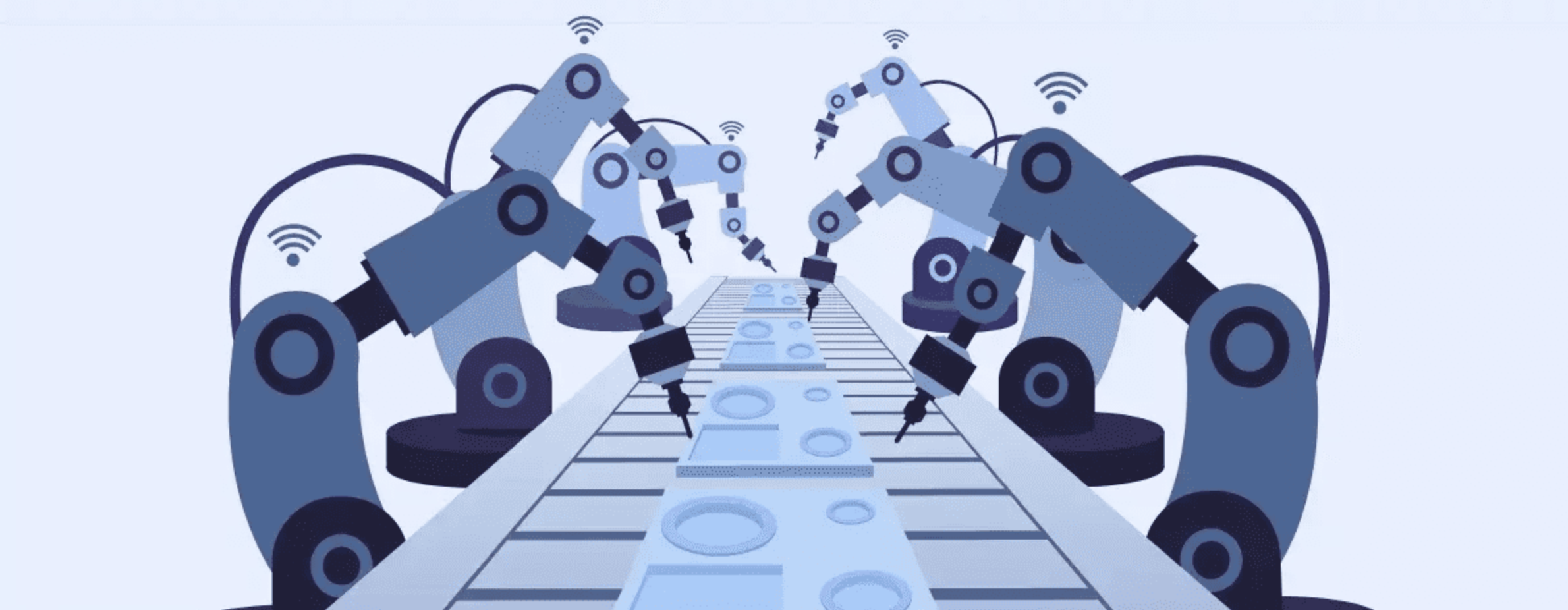
Benefits of Manufacturing Workflow Automation
Implementing manufacturing workflow automation offers numerous potential benefits:
Improved efficiency and productivity - Automating repetitive manual tasks allows manufacturers to boost throughput and reduce cycle times. Smart scheduling maximizes utilization of production assets.
Higher quality - Automated inspection and monitoring reduces defects and errors. Predictive maintenance prevents unplanned downtime and failures.
Enhanced flexibility and responsiveness - Dynamic production routing and inventory optimization allows for on-demand changes. Automation accommodates custom orders and production mixes.
Better visibility and control - Real-time data on assets, orders, inventory, etc. gives clearer operational visibility. Analytics turns data into actionable insights.
Lower costs - Increased throughput, uptime, and quality drive cost reductions. Automation also reduces labor expenses associated with manual processes.
According to ARC Advisory Group, manufacturers implementing workflow automation can expect 10-20% improvements in productivity, 20-50% reductions in unplanned downtime, 30-50% reductions in scrap and rework rates, and 20-30% reductions in inventory costs.
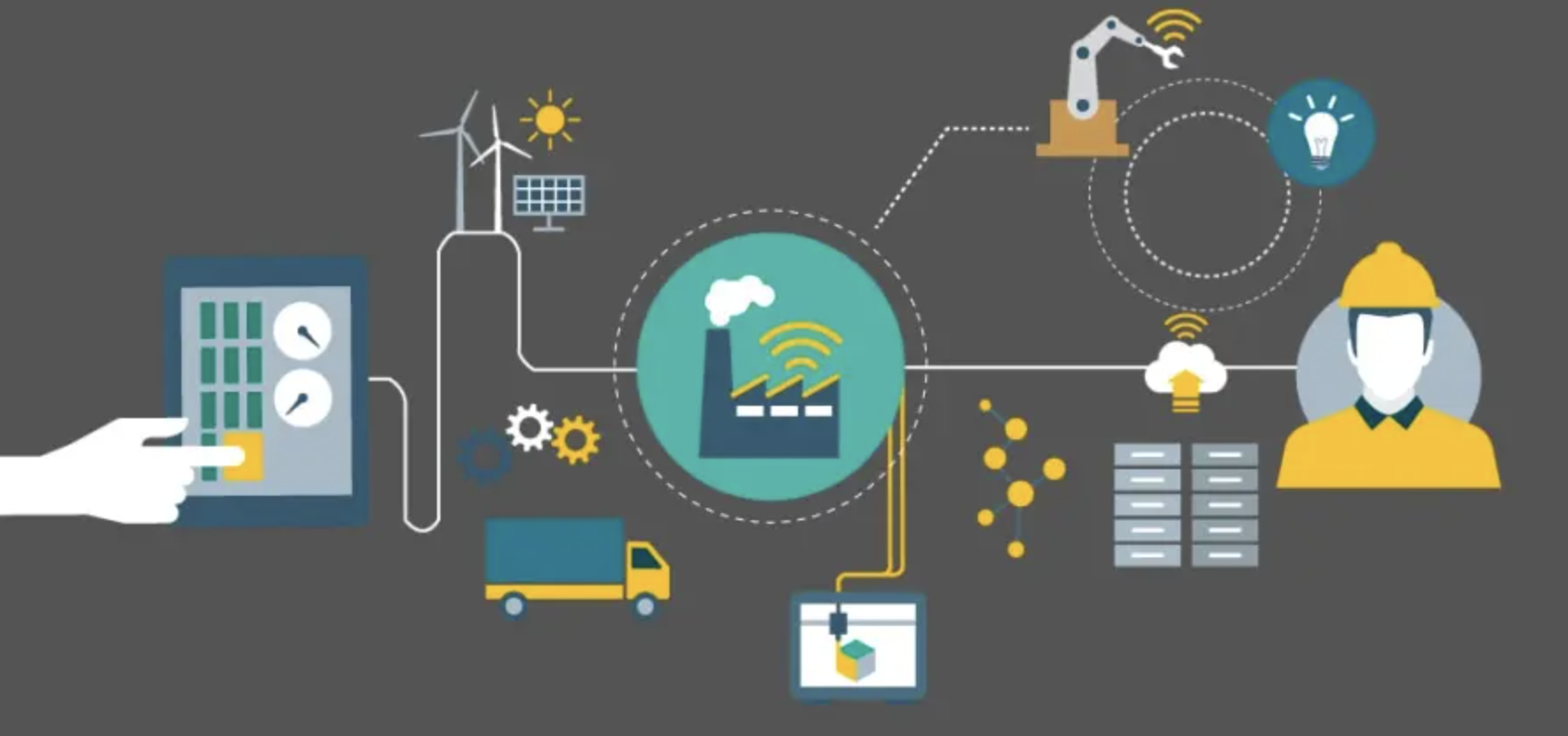
Examples of Manufacturing Workflow Automation
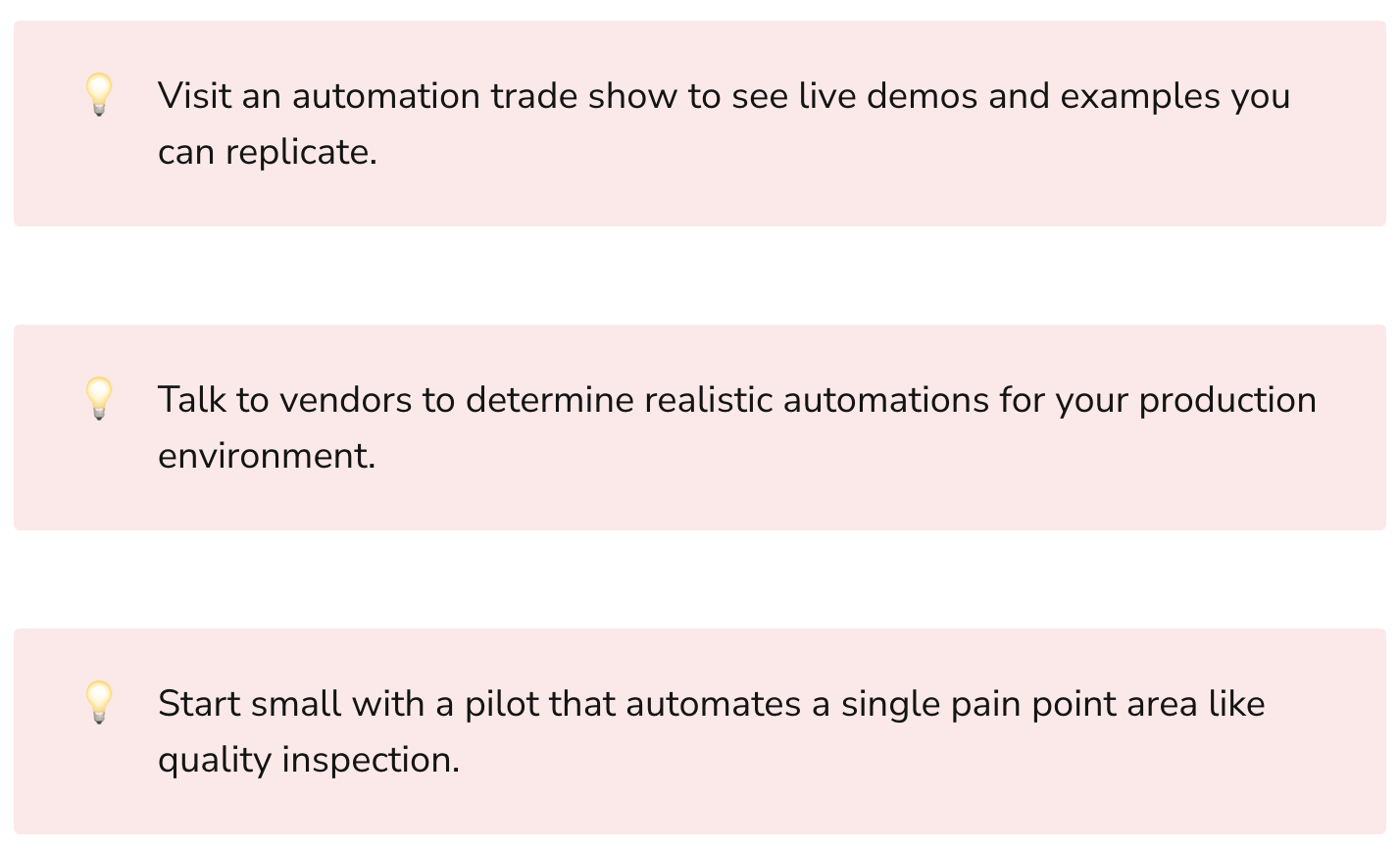
Manufacturing workflow automation can be applied across nearly all production processes. Here are some examples:
Assembly Line Optimization
Automating assembly line functions like production scheduling, sequencing, material handling, quality control, and line balancing. For example:
- Order management software analyzes orders and optimally schedules production runs.
- Sensors track material inventory and trigger restocking when items are low.
- Pick-and-place robots assist with repetitive assembly tasks.
- Machine vision systems perform quality inspection for defects.
- Analytic algorithms adjust conveyor speeds dynamically to maximize output.
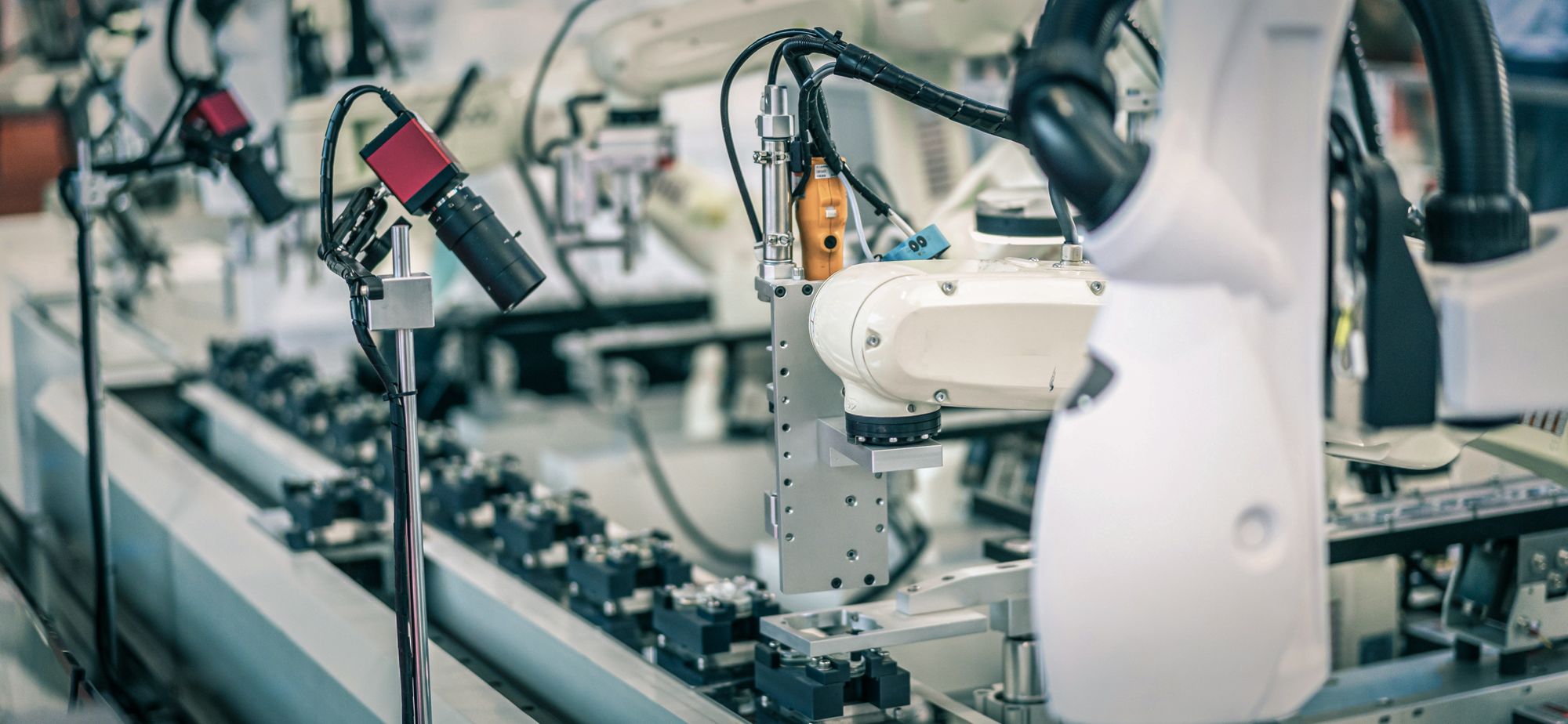
Inventory and Warehouse Management
Automating tracking of inventory, supplies, and equipment. For example:
- RFID tags track inventory levels across the warehouse in real-time.
- Optimization algorithms schedule and route material deliveries.
- Automated storage and retrieval systems pick, pack, and move items efficiently.
- Predictive algorithms trigger automatic re-orders when supplies are running low.
Predictive Maintenance and Asset Management
Automating monitoring of production assets to maximize uptime. For example:
- Sensors monitor asset health (vibration, temperature, etc.) and send telemetry data.
- Analytics detect patterns indicative of impending failures and trigger maintenance.
- Workflow software schedules and dispatches technicians for repairs optimally.
- Digital twins mirror the real-time status of assets virtually.
Quality Control and Compliance
Automating procedures to ensure quality and meet compliance requirements. For example:
- Automated inspection systems scan items for defects.
- Information systems track genealogy and traceability of items.
- Laboratory information management systems (LIMS) automate testing workflows.
- Compliance software ensures procedures adhere to regulatory requirements.
Supply Chain and Logistics
Automating the flow of materials inbound and outbound from manufacturing. For example:
- IoT sensors track location and condition of items in transit.
- Software optimizes transportation routes and schedules.
- Automated warehouses manage inbound/outbound shipments.
- ERP integration links logistics data with production systems.
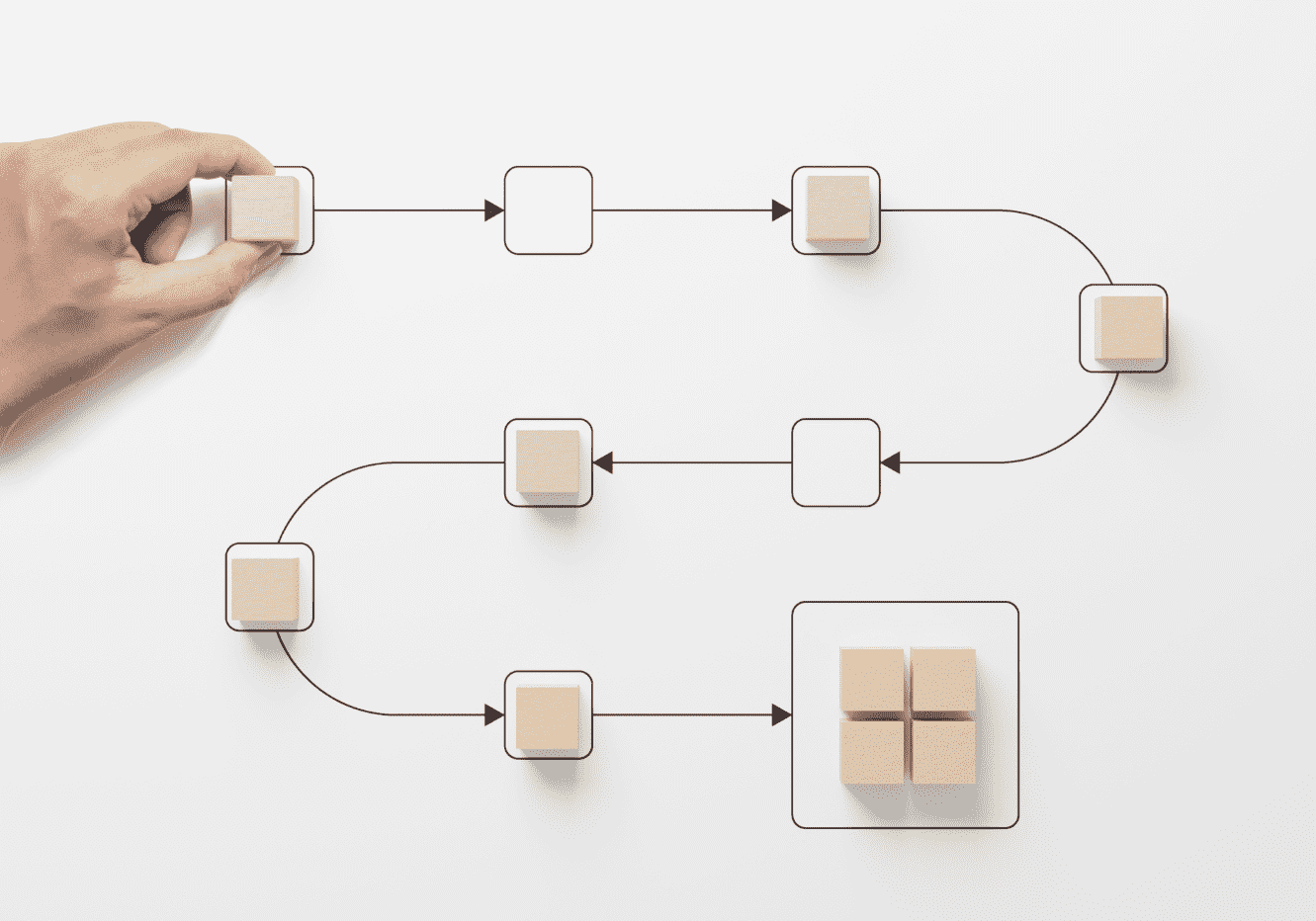
Challenges of Manufacturing Workflow Automation
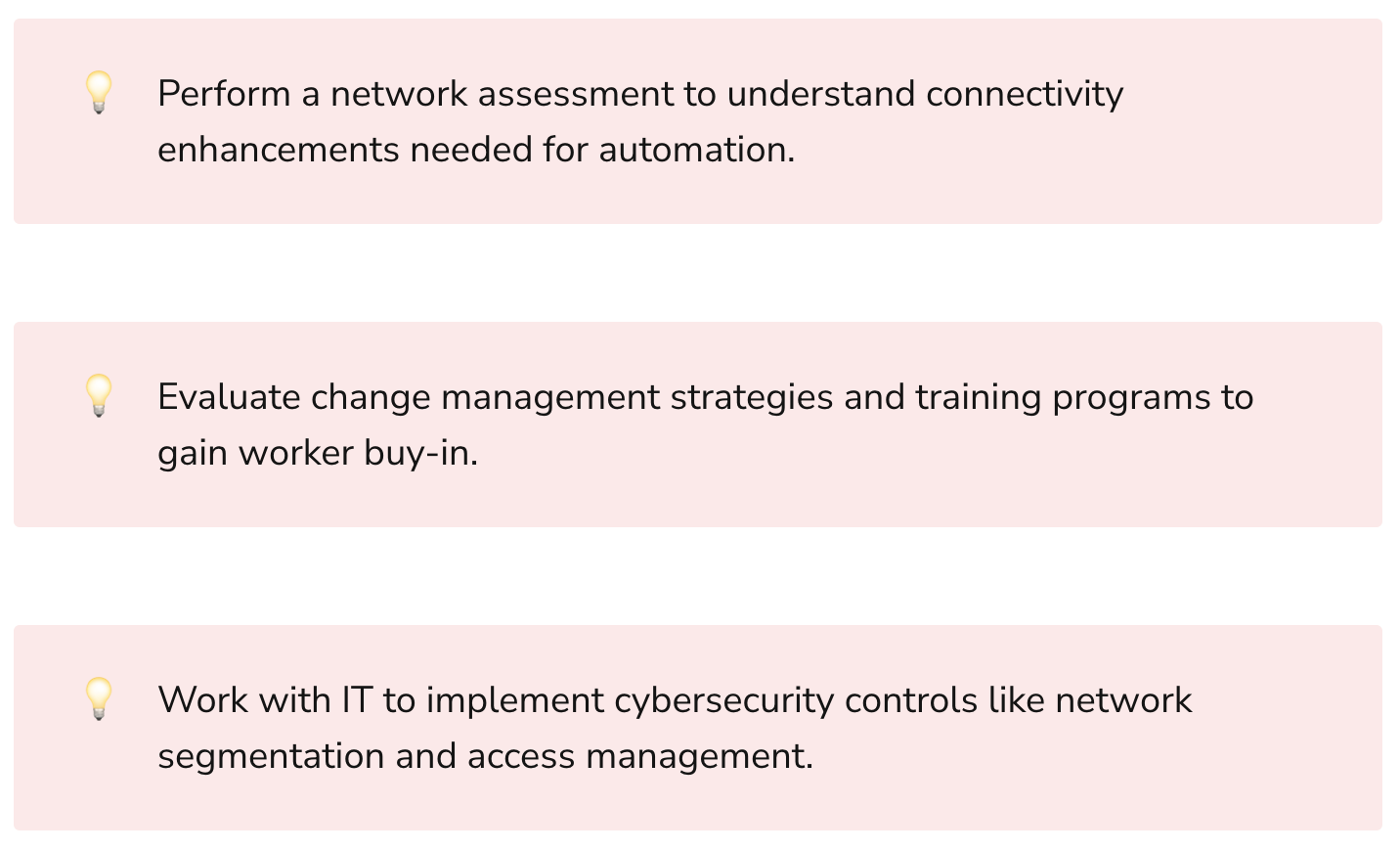
While manufacturing automation holds great promise, it also poses some key implementation challenges:
Integration - New automation tools must integrate with legacy factory hardware and software. Lack of interoperability can hinder adoption.
Data management - Collecting, normalizing, and analyzing vast amounts of real-time data is challenging. Manufacturers must ensure data quality and availability.
Change management - Workers may resist automation that changes job roles and responsibilities. Proper change management and training is critical.
Cybersecurity - Connecting industrial assets increases cyber risks. Security must be incorporated into automated systems.
Upfront costs - While automation improves roi in the long run, upfront costs can deter adoption, especially for smaller manufacturers. Justifying costs is key.
Technical expertise - Most manufacturers lack the software and analytics talent needed to build and maintain complex automated systems. Partnering with automation integrators and vendors helps overcome this barrier.
Onboarding complexity - Getting started with workflow automation can seem daunting. Manufacturers benefit from an incremental roadmap focused on pain points versus a broad overhaul.
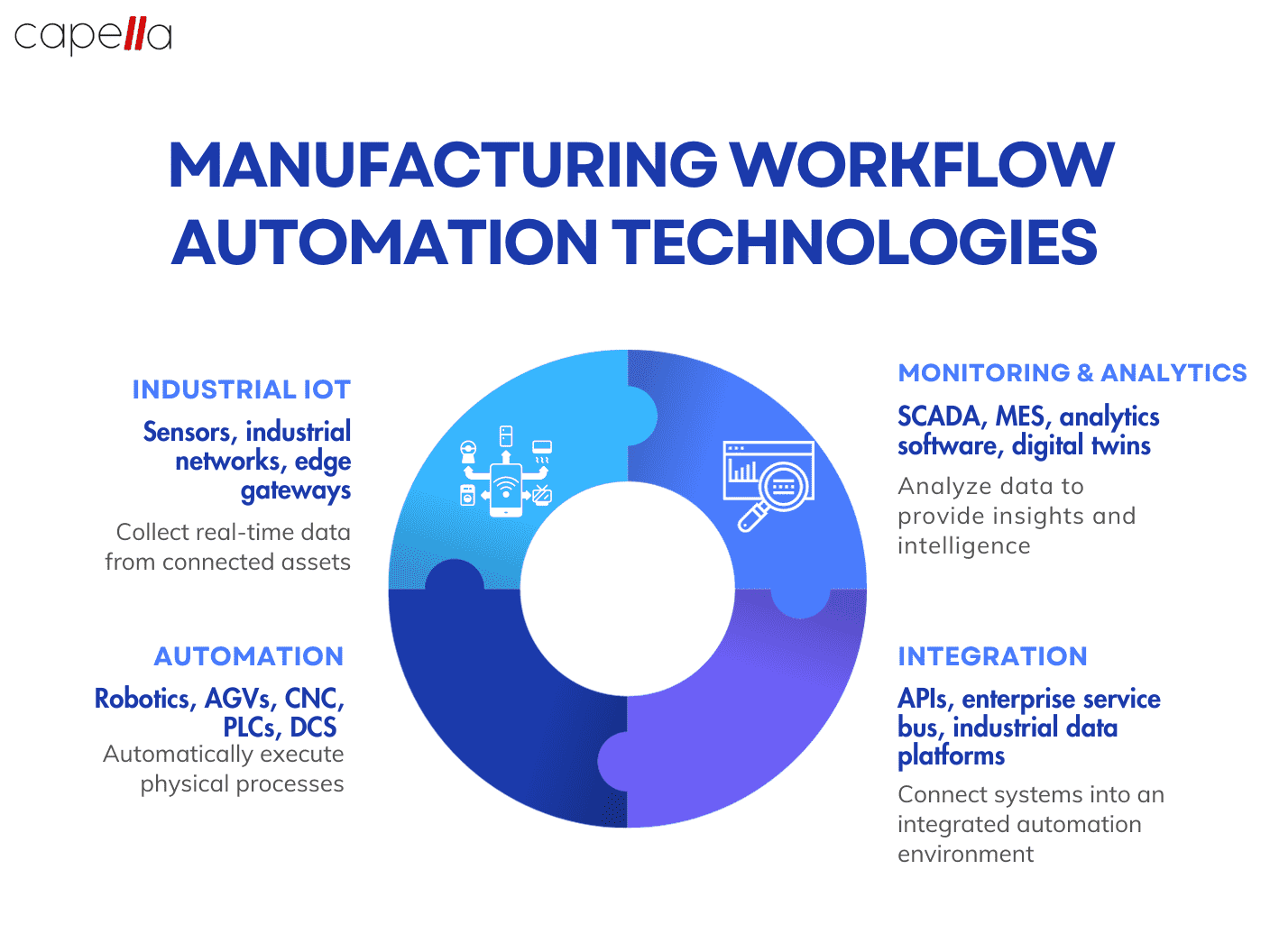
Manufacturing Workflow Automation Technologies
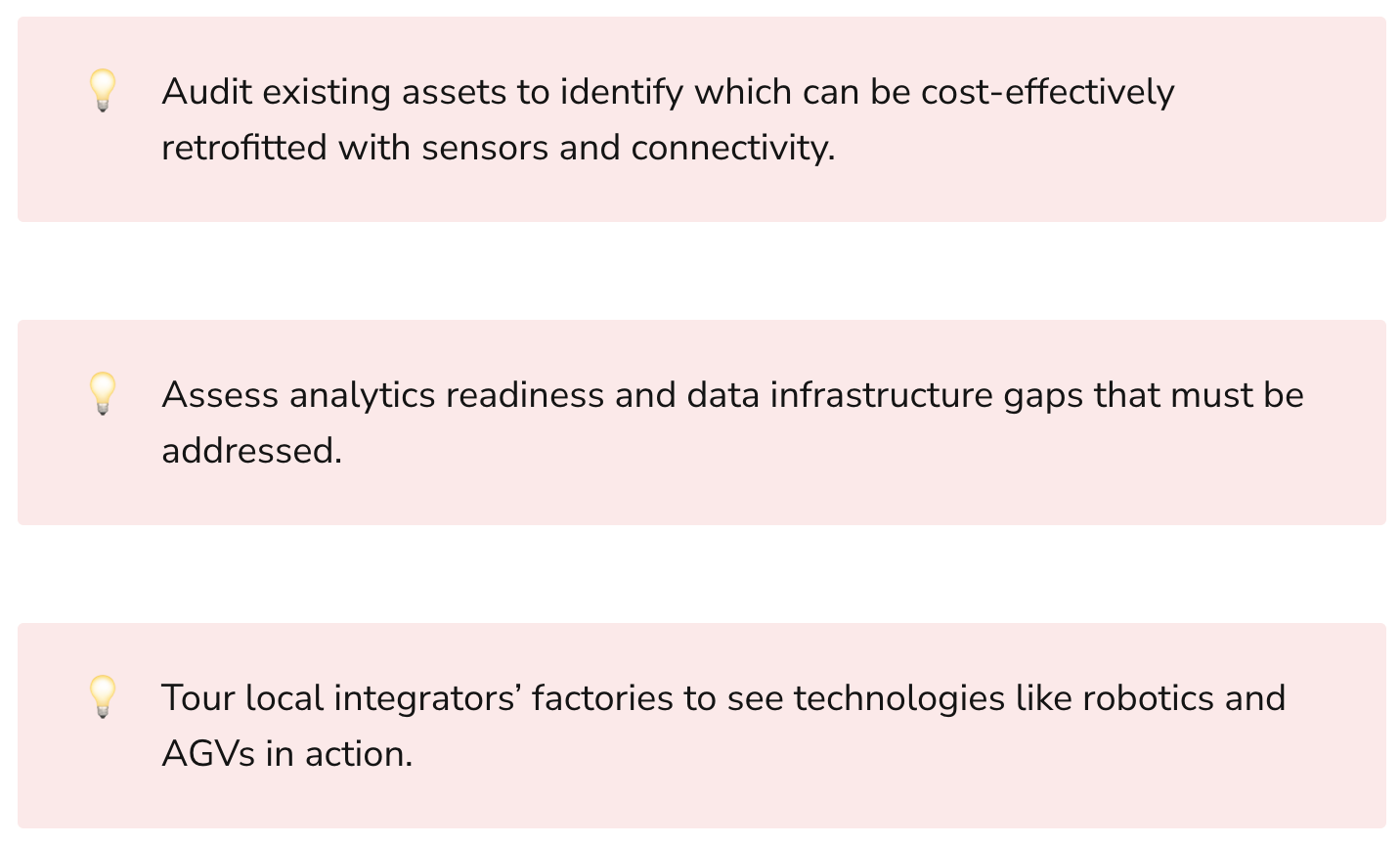
A variety of technologies come together to enable smart manufacturing workflow automation. Some key categories include:
Industrial IoT and Connectivity
Networks that connect manufacturing assets to collect sensor data and enable industrial internet of things (IIoT) capabilities. For example:
- Sensors - Measure temperature, pressure, vibration, electrical currents, sound, image, and other telemetry from assets.
- Industrial networks - Wired and wireless networking hardware and protocols (Ethernet, WiFi, cellular, etc.).
- Connectivity platforms - Edge gateways, I/O modules, and software to network and manage assets.
Monitoring, Analytics, and Intelligence
Software tools that contextualize, analyze, and act on manufacturing data. For example:
- SCADA systems - Monitor real-time data from connected assets.
- MES/MOM systems - Collect production data and support workflow automation.
- Analytics software - Apply statistical methods, machine learning, and AI to find insights.
- Digital twin software - Create virtual models of assets that mirror real-time data.
Automation and Control Technologies
Hardware and software to automate physical manufacturing processes. For example:
- Robotics - Industrial robots that automate material handling, assembly, welding, painting, inspection, and more.
- Conveyors/AGVs - Automated guided vehicles and conveyor systems that move materials.
- CNC Machines - Computer numerical control (CNC) machines that execute automated machining.
- PLCs - Programmable logic controllers (PLCs) that automate equipment control.
- DCS/SCADA - Distributed control systems (DCS) and supervisory control and data acquisition (SCADA) software to automate workflows.
Integration Middleware
Software “glue” that connects automation technologies together into an integrated system. For example:
- APIs - Application programming interfaces (APIs) that enable software-to-software connectivity.
- Enterprise service buses - Middleware to integrate disconnected systems.
- Industrial data platforms - Cloud platforms that contextualize and connect siloed data sources.
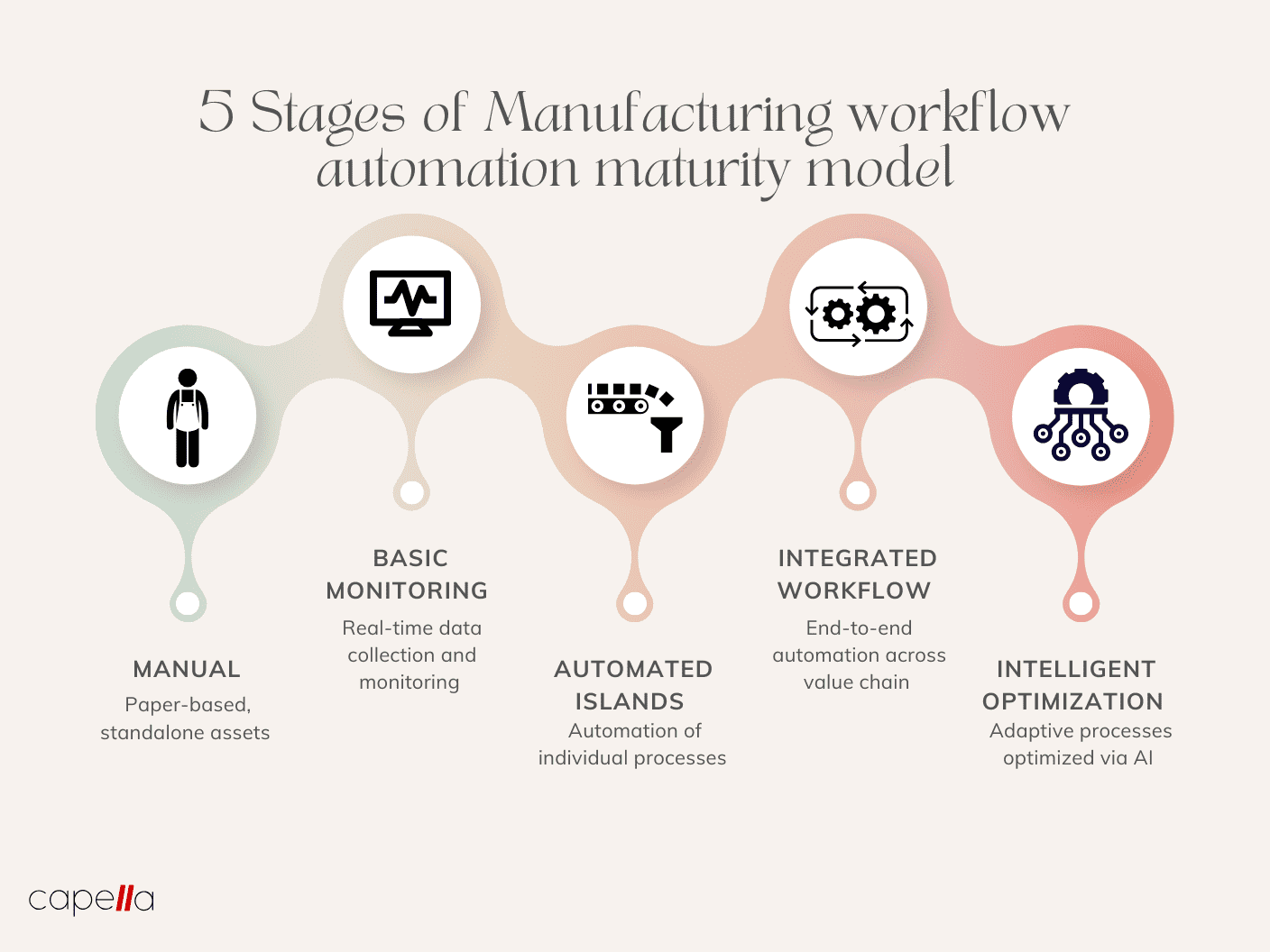
Manufacturing Workflow Automation Use Cases
Manufacturing workflow automation delivers value across many common production use cases:
Production Scheduling and Sequencing
Automatically schedule production runs and sequence jobs on the factory floor for optimal flow.

Benefits:
- Increase capacity utilization by ~20%
- Cut lead times by 50% or more
- Enable just-in-time production flows
Predictive Maintenance
Monitor asset condition and predict maintenance needs before failure.

Benefits:
- Reduce unplanned downtime by 30-50%
- Cut maintenance costs by 25% or more
- Extend asset lifetime
Quality Optimization
Automate inspection and adjust processes to minimize defects.

Benefits:
- Slash scrap and rework by 40% or more
- Reduce costs of manual inspections
- Consistent high quality output
Inventory Optimization
Use real-time data to optimize inventory levels and locations.

Benefits:
- Cut excess inventory by 30% or more
- Reduce stockouts and line stoppages
- Lower warehousing costs
Recommendations for Getting Started with Manufacturing Workflow Automation
Here are some best practices manufacturers should consider when starting out on an automation journey:
Focus on pain points - Let pain guide priorities. Start by automating high-impact bottleneck processes vs. trying to overhaul everything at once. Quick wins build momentum.
Leverage existing data - Manufacturers often already collect vast amounts of data that can fuel automation initiatives without new infrastructure. Start analyzing what you already have.
Evaluate partnerships - Many manufacturers lack internal capabilities to build automated systems. Strategic partnerships with automation integrators and equipment vendors can supplement expertise.
Take an iterative approach - View automation as an ongoing journey of continuous improvement, not a one-time project. Iteratively expand use cases and extend value.
Plan for change management - Involve frontline workers early and often. Reskilling and training helps gain buy-in. Change takes time.
Assess cybersecurity risks - Connecting industrial environments necessitates cybersecurity protections like network segmentation, access controls, and endpoint security.
Explore financing options - Automation requires upfront investment that pays back over time. Leasing, loans, and automation-as-a-service models spread out costs.
The Future of Smart Manufacturing
Manufacturing workflow automation is a pivotal part of Industry 4.0 - the ongoing evolution towards smart, connected factories. As technology continues advancing, manufacturers will be able to automate ever-more complex processes. Human operators, automated systems, robots, and AI algorithms will collaborate seamlessly across dynamic production environments.
While automation will disrupt some manufacturing roles, it will also create new opportunities. Workers will spend less time on repetitive tasks and more time monitoring processes, troubleshooting issues, and continuously improving operations. Management roles will increasingly focus on maximizing value from automation technologies and data-driven decision making.
The factories of the future will be remarkably efficient, flexible, and optimized to meet the on-demand needs of the business. Production will shift from being project-driven to product-driven, with the ability to economically produce highly customizable and personalized products. Automation will drive a manufacturing renaissance - allowing local production to flourish across markets worldwide.
The journey towards smart manufacturing powered by workflow automation has only just begun. Manufacturers that embrace this shift today will be best positioned to lead the factories of the future.
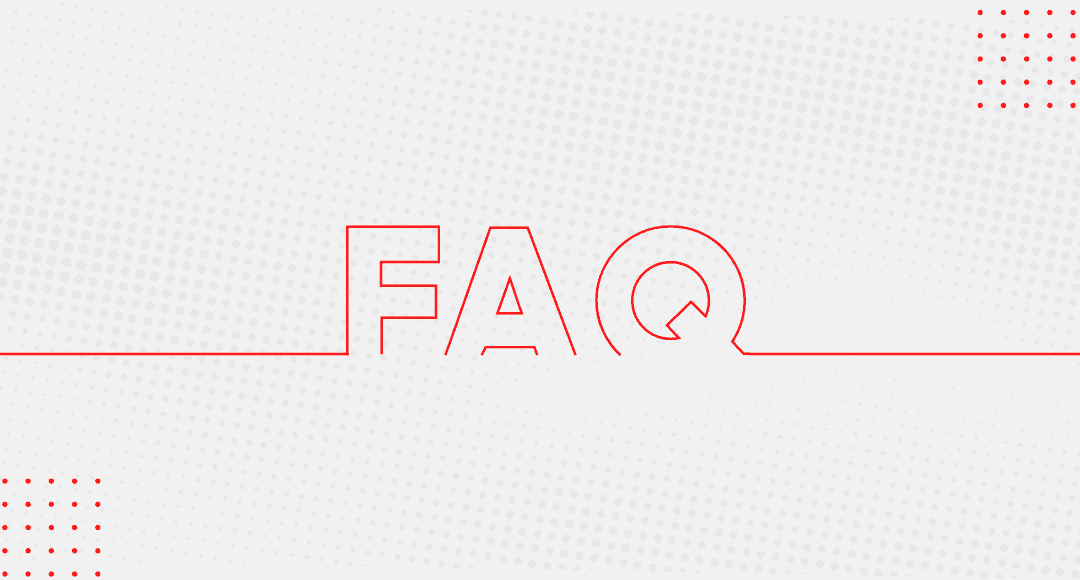
What are some common use cases for manufacturing workflow automation?
Manufacturing workflow automation has many use cases that span production processes. Some of the most common examples include:
- Production scheduling & sequencing - Software can automatically schedule jobs and optimize sequencing on the floor to maximize flow and output. This allows dynamic re-scheduling when new orders come in or disruptions occur.
- Quality optimization - Automated inspection systems combined with data analytics provide real-time quality control and defect reduction capabilities. Issues can trigger alerts and adjustments to improve quality.
- Predictive maintenance - By monitoring asset sensor data and applying algorithms to detect issues before they occur, manufacturers can minimize unplanned downtime and reduce maintenance costs.
- Inventory optimization - Real-time inventory tracking and analytics help optimize stock levels and locations. Automated re-order and stocking processes also boost efficiency.
- Supply chain integration - Tying logistics data into production workflows allows for tighter coordination across the value chain. This improves material availability and reduces expedited shipping costs.
What are some key benefits manufacturers see from implementing workflow automation?
The benefits are wide-ranging and include:
- Increased production throughput and capacity utilization by 20% or more
- Reduced cycle times and lead times - 50% reductions or greater are common
- Lower defect and scrap rates - automation can reduce these by 40%+
- Less unplanned downtime - 30-50% reductions are typical
- Improved inventory management - automation can cut excess stocks by 30%+
- Higher production consistency and repeatability
- Better labor efficiency - staff spend less time on manual tasks and firefighting issues
- Enhanced quality control and compliance
- Greater manufacturing flexibility - automation allows easy accommodation of new products, order changes etc.
In total, many manufacturers see a 10-20% increase in key metrics like productivity and profitability following automation initiatives.
What are some challenges companies face when implementing manufacturing workflow automation?
Some common challenges faced when implementing automation include:
- Integration with legacy systems - Lack of interoperability and standards can make connecting automation tools to existing factory hardware/software difficult.
- Managing data - Collecting, contextualizing, and analyzing huge volumes of real-time data from sensors and systems is challenging. Ensuring quality and availability is critical.
- Change management - Workers may resist changes to processes and responsibilities. Strong leadership and communication is key to gain buy-in.
- Cybersecurity - Connecting industrial environments necessitates robust protections including network segmentation, access controls, and endpoint security.
- Costs - The upfront investment required for automation can deter small/medium manufacturers. Creative financing options can help.
- Expertise gaps - Most manufacturers lack the skills needed to develop and support automated systems. Partnering with integrators and vendors helps close this gap.
What are some tips for getting started with manufacturing workflow automation?
Some best practices to consider when starting an automation initiative:
- Start small - Focus the initial pilot on a single pain point process vs. a full overhaul. Demonstrate quick wins to build momentum.
- Leverage existing data - Manufacturers often already collect valuable data that can fuel automation without new infrastructure. Start analyzing it.
- Take an iterative approach - View automation as a continuous journey vs. one-time project. Incrementally expand use cases.
- Assess partnerships - Work with automation integrators and equipment vendors to supplement internal expertise as needed.
- Plan for change management - Involve frontline staff early and often. Invest in reskilling and training.
- Consider security - Account for cybersecurity needs like network controls and endpoint management as part of the design.
- Explore financing - Automation requires upfront investment with long-term payback. Leasing and "as-a-service" models can help.
What types of sensors are commonly used for manufacturing workflow automation?
Industrial sensors measure parameters like temperature, pressure, flow, vibration, electrical current, sound, and imagery. Common examples include:
- Temperature - Thermocouples, thermistors, infrared
- Pressure - Piezoelectric, capacitive, strain gauge
- Flow - Coriolis, turbine, magnetic, ultrasonic
- Vibration - Accelerometers, proximity probes
- Current - Current transformers, shunt resistors
- Voltage - Potential transformers
- Sound - Microphones, hydrophones
- Image - Area scan cameras, line scan cameras
- Presence/Proximity - Limit switches, proximity sensors
Choosing the right sensors requires assessing the environment, performance needs, accuracy, and connectivity requirements. Hardwired sensors connect to PLCs while wireless options like Bluetooth and WiFi enable IoT capabilities.
What types of software platforms enable manufacturing workflow automation?
Several types of software come together to enable automation:
- SCADA - Supervisory Control and Data Acquisition software visualizes real-time data and operator interactions.
- MES - Manufacturing Execution Systems manage production dispatching, quality, performance, inventory etc.
- ERP - Enterprise Resource Planning systems handle order management, planning, logistics.
- PLC - Programmable Logic Controllers automate machine and process control.
- DCS - Distributed Control Systems regulate production equipment and environments.
- Analytics - Manufacturing analytics platforms derive insights from production data.
- Digital Twin - Software creates virtual models of assets that mirror real-time data.
These solutions integrate through standard interfaces or enterprise service buses. Cloud platforms are increasingly providing easy access to these capabilities via SaaS models.
How can manufacturers justify the business case for automation investments?
Building a compelling business case requires quantifying the expected return from automation such as:
- Increased throughput - e.g. "20% more product units per day"
- Faster cycle times - e.g. "Reduce cycle by 50%"
- Less downtime - e.g. "Reduce downtime by 30% saving us $X per year"
- Higher yield - e.g. "Improve first pass yield by 10% saving $X in scrap"
- Inventory reduction - e.g. "Cut excess inventory by 20% freeing up $X in working capital"
- Labor savings - e.g. "Eliminate 10 FTEs involved in manual quality inspection"
Financial metrics like ROI, NPV, and payback period demonstrate how the savings and benefits above translate to bottom line impact.
Piloting on a small scale first makes the benefits tangible. Starting with pain points that align with business goals helps secure leadership support.
What are some examples of entry-level manufacturing workflow automations?
Some good entry-level automations include:
- Automating data collection from existing equipment like PLCs into visualization dashboards
- Implementing barcode/RFID tracking for inventory management
- Deploying sensor condition monitoring and alerts on critical assets
- Automating a standalone process like robotic quality inspection after manual assembly steps
- Piloting guided vehicles for material movement in a contained area
- Automating warehouse picking and put-away processes
These demonstrate value without huge upfront investment. Once proven, automation can scale incrementally across the facility over time.
What emerging technologies show promise for manufacturing workflow automation in the future?
Some emerging technologies to watch include:
- AI/ML applications - Increasingly "smart" quality control, predictive maintenance, inventory optimization etc.
- Digital twins - Detailed virtual models of facilities and processes enable simulation and optimization.
- AR/VR - Augmented and virtual reality improve remote management and worker training/assistance.
- 5G - Faster wireless connectivity will accelerate industrial IoT and edge capabilities.
- Autonomous mobile robots - Flexible fleets that can dynamically move materials and collaborate with humans.
- Co-bots - Collaborative robots like "Cobots" work safely alongside people without barriers.
- Additive mfg - 3D printing integration directly from digital designs will disrupt production flows.
These technologies will enable the smart, flexible factories of the future as automation evolves from fixed tooling to dynamically reconfigurable systems.
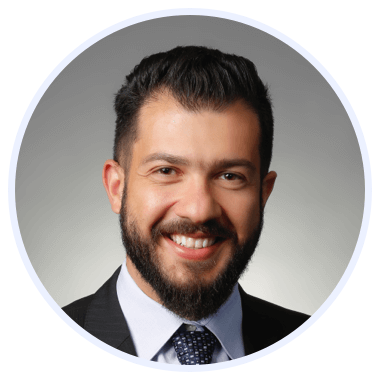
Rasheed Rabata
Is a solution and ROI-driven CTO, consultant, and system integrator with experience in deploying data integrations, Data Hubs, Master Data Management, Data Quality, and Data Warehousing solutions. He has a passion for solving complex data problems. His career experience showcases his drive to deliver software and timely solutions for business needs.